Three-cycle desulphurization method for wet type ammonia-process desulphurization and flue gas desulfurization tower or system
A technology of ammonia desulfurization and three cycles, applied in separation methods, chemical instruments and methods, gas treatment, etc., can solve the problems of ignoring the oxidation and crystallization of by-products, uneconomical operation, uneven distribution of flue gas, etc., and achieve reduction The effect of aerosol and ammonia escape, reducing energy consumption and operating costs, and improving air distribution
- Summary
- Abstract
- Description
- Claims
- Application Information
AI Technical Summary
Problems solved by technology
Method used
Image
Examples
Embodiment 1
[0046] Such as figure 1 As shown, the three-cycle flue gas desulfurization tower for wet ammonia desulfurization of the present invention is a single tower, and the desulfurization tower is ¢5000×H30000, and the flue gas inlet 1 to the flue gas outlet 11 of the desulfurization tower are sequentially The first-stage absorption zone I, the second-stage absorption zone II and the washing zone III are arranged upwards, wherein the flue gas inlet 1 is located in the middle and lower part of the first-stage absorption zone, and the flue gas outlet 11 is located at the top of the washing zone.
[0047] The first-stage absorption zone is correspondingly provided with a first slurry circulation loop, and the first slurry circulation loop includes a first slurry spray layer 2 and a first slurry circulation pump 13; the first slurry spray layer 2 is horizontally arranged In the desulfurization tower; the inlet of the first slurry circulating pump 13 communicates with the bottom of the de...
Embodiment 2
[0054] Such as figure 2 As shown, the three-cycle flue gas desulfurization system for wet ammonia desulfurization of the present invention, the desulfurization system is a double tower, including a pre-washing tower 23 and a main absorption tower 24, the first pre-washing tower 23 is provided with a first First-stage absorption zone I, the lower part of the main absorption tower 24 is provided with a second-stage absorption zone II, and the upper part is provided with a washing zone III; the first-stage absorption zone communicates with the second-stage absorption zone through a connecting smoke pipe 18 ; The flue gas inlet 1 of the desulfurization system is located at the lower part of the first-stage absorption zone, and the flue gas outlet 11 is located at the top of the washing zone;
[0055] The first-stage absorption zone is correspondingly provided with a first slurry circulation loop, and the first slurry circulation loop includes a first slurry spray layer 2 and a fi...
PUM
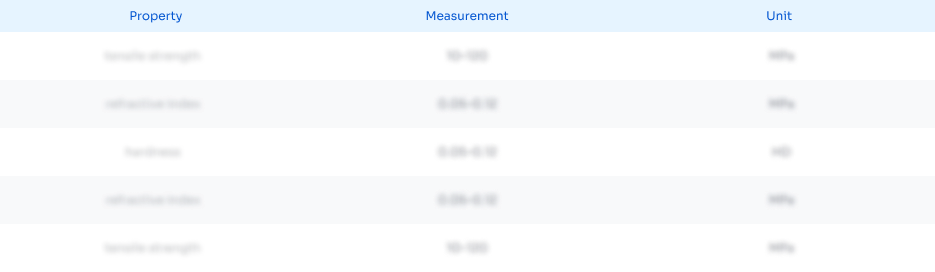
Abstract
Description
Claims
Application Information

- R&D
- Intellectual Property
- Life Sciences
- Materials
- Tech Scout
- Unparalleled Data Quality
- Higher Quality Content
- 60% Fewer Hallucinations
Browse by: Latest US Patents, China's latest patents, Technical Efficacy Thesaurus, Application Domain, Technology Topic, Popular Technical Reports.
© 2025 PatSnap. All rights reserved.Legal|Privacy policy|Modern Slavery Act Transparency Statement|Sitemap|About US| Contact US: help@patsnap.com