Basalt continuous fiber furnace with bottom-inserted electrode
A continuous fiber and basalt technology is applied in the field of electro-melting preparation of basalt continuous fibers, which can solve the problems of high production cost, many product quality defects, and low service life of the kiln, so as to improve quality, improve melting efficiency, and reduce melting The effect of energy consumption
- Summary
- Abstract
- Description
- Claims
- Application Information
AI Technical Summary
Problems solved by technology
Method used
Image
Examples
Embodiment Construction
[0016] Below in conjunction with specific embodiment, further illustrate the present invention. It should be understood that these examples are only used to illustrate the present invention and are not intended to limit the scope of the present invention. In addition, it should be understood that after reading the teachings of the present invention, those skilled in the art can make various changes or modifications to the present invention, and these equivalent forms also fall within the scope defined by the appended claims of the present application.
[0017] Embodiments of the present invention relate to a bottom inserted electrode basalt continuous fiber kiln, such as figure 1 As shown, a melting pool 2 is included, and the melting pool 2 is provided with a feed port 1; a rod-shaped molybdenum electrode 6 is inserted into the bottom of the melting pool 2, and a cooling device 5 is placed on the rod-shaped molybdenum electrode 6. The electrodes 6 are connected to the Scott ...
PUM
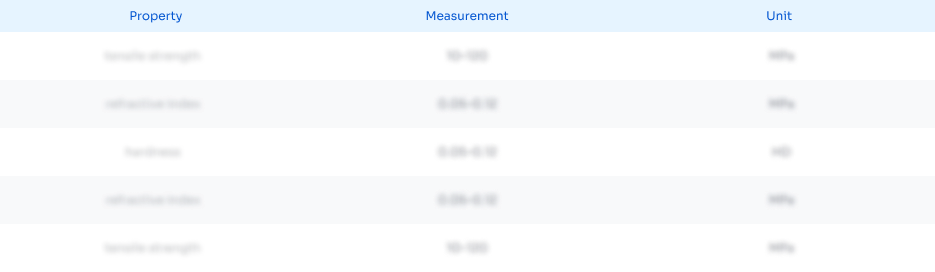
Abstract
Description
Claims
Application Information

- R&D
- Intellectual Property
- Life Sciences
- Materials
- Tech Scout
- Unparalleled Data Quality
- Higher Quality Content
- 60% Fewer Hallucinations
Browse by: Latest US Patents, China's latest patents, Technical Efficacy Thesaurus, Application Domain, Technology Topic, Popular Technical Reports.
© 2025 PatSnap. All rights reserved.Legal|Privacy policy|Modern Slavery Act Transparency Statement|Sitemap|About US| Contact US: help@patsnap.com