A method for preparing perovskite thin films in perovskite solar cells by solution pumping and ventilating method
A solar cell and perovskite technology, applied in circuits, electrical components, photovoltaic power generation, etc., can solve the problem of unstable solution surface, inability to obtain uniform and dense perovskite films, and inability to effectively control film uniformity and crystallinity, etc. problems, to achieve the effect of reducing battery performance
- Summary
- Abstract
- Description
- Claims
- Application Information
AI Technical Summary
Problems solved by technology
Method used
Image
Examples
Embodiment 1
[0069] 1) With DMF as solvent, PbI 2 and CH 3 NH 3 I is the solute, and the perovskite solution is prepared, and the CH in the perovskite solution 3 NH 3 PB 3 The mass percentage concentration is 35%.
[0070] 2) A layer of prepared perovskite solution was sprayed on the flexible conductive substrate ITO by spraying method to obtain a layer of light yellow perovskite liquid film with a thickness of about 1500nm.
[0071] 3) Exhaust and dry at 50°C. At this temperature, the saturated vapor pressure of the solvent is about 2200Pa. The perovskite liquid film is placed in a chamber of 400Pa. At this time, the pressure difference between the solvent and the chamber pressure is 1800Pa. The solvent evaporates quickly, and the liquid film has a very high degree of supersaturation, which satisfies the conditions for nucleation, and the liquid film nucleates and grows heterogeneously on the rough substrate. In the drying process, in order to avoid the solvent vapor from corroding ...
Embodiment 2
[0075] 1) With DMSO as solvent, PbI 2 and CH 3 NH 3 I is the solute, and the perovskite solution is prepared, and the CH in the perovskite solution 3 NH 3 PB 3 The mass percentage concentration is 30%.
[0076] 2) Scrape-coat a layer of prepared perovskite solution on the conductive glass FTO substrate to obtain a layer of light yellow perovskite liquid film with a thickness of about 2000nm.
[0077] 3) Air extraction and drying are carried out at 70°C. At this temperature, the saturated vapor pressure of the solvent is about 5900Pa. The perovskite liquid film is placed in a chamber of 40Pa. At this time, the pressure difference between the solvent and the chamber pressure is 5860Pa. After the solvent evaporates, the liquid film reaches supersaturation, and the liquid film nucleates and grows heterogeneously on the surface of the rough substrate. In the drying process, in order to avoid the solvent vapor from corroding the film, nitrogen gas with a DMSO partial pressure ...
Embodiment 3
[0081] 1) With DMF as solvent, PbI 2 and CH 3 NH 3 I is the solute, and the perovskite solution is prepared, and the CH in the perovskite solution 3 NH 3 PB 3 The mass percentage concentration is 45%.
[0082] 2) Spraying a layer of prepared perovskite solution on the glass conductive substrate ITO by coating method to obtain a layer of light yellow perovskite liquid film with a thickness of about 5000nm.
[0083] 3) Air extraction and drying are carried out at 30°C. At this temperature, the saturated vapor pressure of the solvent is about 740Pa. The perovskite liquid film is placed in a chamber of 600Pa. At this time, the pressure difference between the solvent and the chamber pressure is 140Pa. The solvent evaporates quickly, and the liquid film has a very high degree of supersaturation, which satisfies the conditions for nucleation, and the liquid film nucleates and grows heterogeneously on the rough substrate. During the drying process, in order to avoid the solvent ...
PUM
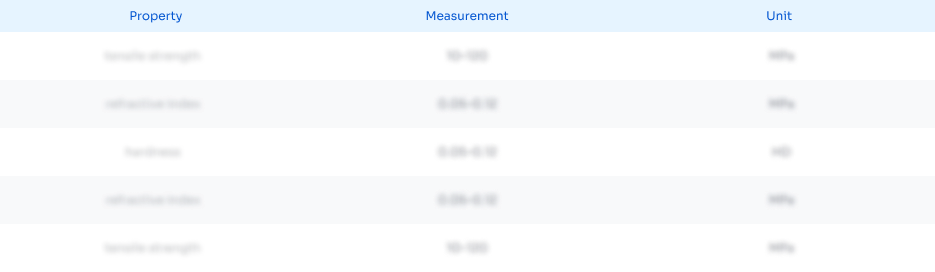
Abstract
Description
Claims
Application Information

- R&D
- Intellectual Property
- Life Sciences
- Materials
- Tech Scout
- Unparalleled Data Quality
- Higher Quality Content
- 60% Fewer Hallucinations
Browse by: Latest US Patents, China's latest patents, Technical Efficacy Thesaurus, Application Domain, Technology Topic, Popular Technical Reports.
© 2025 PatSnap. All rights reserved.Legal|Privacy policy|Modern Slavery Act Transparency Statement|Sitemap|About US| Contact US: help@patsnap.com