Method for prolonging service life of polycrystalline silicon chip minority carrier and reducing dislocation of polycrystalline silicon chip
A polycrystalline silicon wafer and minority carrier lifetime technology, which is applied in chemical instruments and methods, polycrystalline material growth, crystal growth and other directions, can solve the problems of polycrystalline silicon wafers such as larger grain size, low production cost, and minority carrier unevenness. Uniform and low problems, solving the effect of grain enlargement and dislocation increase, reducing production cost
- Summary
- Abstract
- Description
- Claims
- Application Information
AI Technical Summary
Problems solved by technology
Method used
Examples
Embodiment 1
[0102] A method for improving the minority carrier lifetime of polycrystalline silicon wafers and reducing dislocations of polycrystalline silicon wafers, comprising the following steps: (1) preparing raw materials, loading the raw materials into a crucible and sending them into an ingot furnace; (2) performing a heating process; (3) carrying out Melting process; (4) crystal growth process; (5) annealing process; (6) cooling process, after cooling, open the ingot furnace to obtain polycrystalline ingots;
[0103] 1) The step (1) raw material preparation weight ratio is: 50% of primary polycrystalline, 35% of single polycrystalline recycled material, 5% of single polycrystalline fragments, 10% of purified square rod, the primary polycrystalline includes primary Polycrystalline (greater than 6N), secondary and tertiary primary polycrystalline, primary polycrystalline granular materials, single and polycrystalline recycled materials include silicon ingot head material, tail materi...
Embodiment 2
[0144] A method for improving the minority carrier lifetime of polycrystalline silicon wafers and reducing dislocations of polycrystalline silicon wafers, comprising the following steps: (1) preparing raw materials, loading the raw materials into a crucible and sending them into an ingot furnace; (2) performing a heating process; (3) carrying out Melting process; (4) crystal growth process; (5) annealing process; (6) cooling process, after cooling, open the ingot furnace to obtain polycrystalline ingots;
[0145] 1) The step (1) raw material preparation weight ratio is: primary polycrystalline 58%, single polycrystalline recycled material 30%, single polycrystalline fragments 4%, purified square rod 8%, the primary polycrystalline includes primary Polycrystalline (greater than 6N), secondary and tertiary primary polycrystalline, primary polycrystalline granular materials, single and polycrystalline recycled materials include silicon ingot head material, tail material, edge skin...
Embodiment 3
[0186] A method for increasing the minority carrier lifetime of polycrystalline silicon wafers and reducing dislocations of polycrystalline silicon wafers, comprising the following steps: (1) preparing raw materials, loading the raw materials into a crucible and sending them into an ingot furnace; (2) performing a heating process; (3) carrying out Melting process; (4) crystal growth process; (5) annealing process; (6) cooling process, after cooling, open the ingot furnace to obtain polycrystalline ingots;
[0187] 1) The step (1) raw material preparation weight ratio is: primary polycrystalline 65%, single polycrystalline recycled material 25%, single polycrystalline fragments 3%, purified square rod 7%, the primary polycrystalline includes primary Polycrystalline (greater than 6N), secondary and tertiary primary polycrystalline, primary polycrystalline granular materials, single and polycrystalline recycled materials include silicon ingot head material, tail material, edge ski...
PUM
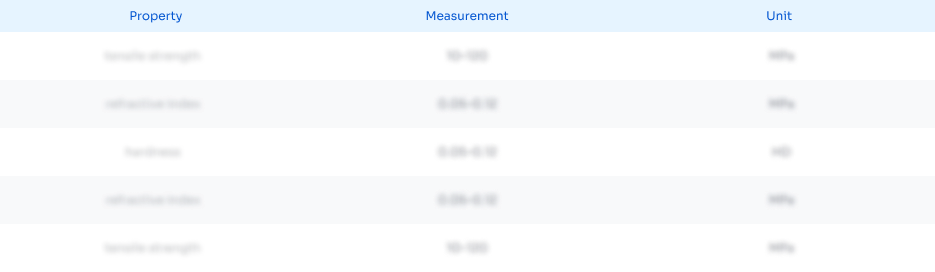
Abstract
Description
Claims
Application Information

- R&D
- Intellectual Property
- Life Sciences
- Materials
- Tech Scout
- Unparalleled Data Quality
- Higher Quality Content
- 60% Fewer Hallucinations
Browse by: Latest US Patents, China's latest patents, Technical Efficacy Thesaurus, Application Domain, Technology Topic, Popular Technical Reports.
© 2025 PatSnap. All rights reserved.Legal|Privacy policy|Modern Slavery Act Transparency Statement|Sitemap|About US| Contact US: help@patsnap.com