Method for preparing spherical lithium/sodium battery negative electrode carbon material
A sodium battery and carbon material technology, applied in battery electrodes, secondary batteries, circuits, etc., can solve the problems of high cost and heavy pollution, and achieve the effects of improving service life, simple preparation process, and improving performance
- Summary
- Abstract
- Description
- Claims
- Application Information
AI Technical Summary
Problems solved by technology
Method used
Image
Examples
preparation example Construction
[0030] A preparation method of spherical lithium / sodium battery negative electrode carbon material, comprising the following steps:
[0031] Step 1: The raw materials are washed, mechanically crushed, and dried at 105°C for 24 hours after being crushed to 1-3 mm; the raw materials are rape husks, rape stalks, rice husks, rice straw, wheat husks, wheat straw, corn stalks, and corn husks , corn cobs or ears of corn;
[0032] Step 2: immerse the dried raw material in a nitric acid solution with a mass concentration of 5-30%, and stir magnetically for 1-48 hours to obtain the solution; wherein, the ratio of the dried raw material to the nitric acid solution is (1.0-3.0) g: 50mL.
[0033] Step 3: Transfer the solution to a polytetrafluoroethylene high-pressure hydrothermal kettle, and conduct a hydrothermal reaction at 120-180°C for 12-24 hours at a speed of 10r / min. The precipitate was washed several times with deionized water and ethanol, and dried at 60°C to obtain the product...
Embodiment 1
[0040] (a) Wash the collected rapeseed shells with deionized water, cut them into 1-3mm pieces, and dry them at 105°C for later use;
[0041] (b) immerse 2.0 g of rape shells in step (a) in 50 mL of nitric acid solution with a mass concentration of 10%, and magnetically stir for 1 h to form a solution;
[0042] (c) Then transfer the solution to a polytetrafluoroethylene high-pressure hydrothermal kettle, and conduct a hydrothermal reaction at 180°C for 24 hours at a speed of 10r / min. After the reaction is complete, cool it to room temperature with the furnace, and wash the precipitate with deionized water and ethanol for several times, and dried at 60°C to obtain the product;
[0043] (d) Put the product in a porcelain boat, carbonize it in an atmosphere furnace, and heat it at 700° C. for 2 hours at a heating rate of 5° C. / min under an argon atmosphere (the argon flow rate is 50 sccm) to obtain a carbonized product;
[0044] (e) further magnetically stirring the carbonized p...
Embodiment 2
[0051] (a) Wash the collected wheat husks with deionized water, cut them into 1-3mm pieces, and dry them at 105°C for later use;
[0052] (b) Soak 3.0 g of wheat husks in 50 mL of 20% nitric acid solution, and stir magnetically for 12 hours to form a solution;
[0053] (c) Then transfer the solution to a polytetrafluoroethylene high-pressure hydrothermal kettle, and conduct a hydrothermal reaction at 180°C for 24 hours at a speed of 10r / min. After the reaction is complete, cool it to room temperature with the furnace, and wash the precipitate with deionized water and ethanol for several times, and dried at 60°C to obtain the product;
[0054] (d) Put the product into a porcelain boat, carbonize it in an atmosphere furnace, and heat it at 600° C. for 2 hours at a heating rate of 10° C. / min under an argon atmosphere (the argon gas flow is 100 sccm) to obtain a carbonized product;
[0055] (e) further treating the carbonized product in a 10% KOH solution at 80° C. for 2 hours, a...
PUM
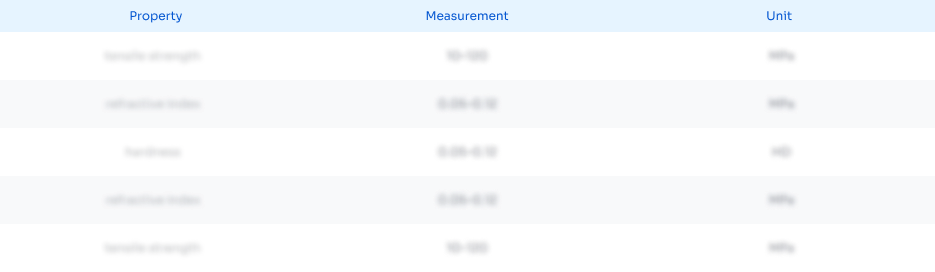
Abstract
Description
Claims
Application Information

- R&D
- Intellectual Property
- Life Sciences
- Materials
- Tech Scout
- Unparalleled Data Quality
- Higher Quality Content
- 60% Fewer Hallucinations
Browse by: Latest US Patents, China's latest patents, Technical Efficacy Thesaurus, Application Domain, Technology Topic, Popular Technical Reports.
© 2025 PatSnap. All rights reserved.Legal|Privacy policy|Modern Slavery Act Transparency Statement|Sitemap|About US| Contact US: help@patsnap.com