Coating thickness measuring method under unknown ultrasonic velocity condition
A coating thickness and measurement method technology, applied in the direction of using ultrasonic/sonic/infrasonic waves, measuring devices, instruments, etc., can solve the problem that the coating thickness cannot be measured
- Summary
- Abstract
- Description
- Claims
- Application Information
AI Technical Summary
Problems solved by technology
Method used
Image
Examples
Embodiment Construction
[0035] The ultrasonic pulse echo detection system used in this method consists of figure 1 The shown USIP40 ultrasonic flaw detector, delay block probe, and computer with MATLAB software installed. The experimental sample in this embodiment is a magnetic loss type radar absorbing coating sample (the absorbent is carbonyl iron powder, the main component of the binder is epoxy resin, and the base material is an aluminum alloy flat plate), the thickness of the coating and the ultrasonic sound velocity Both are unknown quantities, and the ultrasonic pulse echo technology is used to obtain the coating time-domain echo signal, combined with the ultrasonic sound pressure reflection coefficient amplitude spectrum analysis method and the correlation coefficient matching method to simultaneously invert the sample coating thickness and ultrasonic sound velocity. The method employs the following steps:
[0036](a) Sample surface treatment. Use acetone to treat the surface of the coating...
PUM
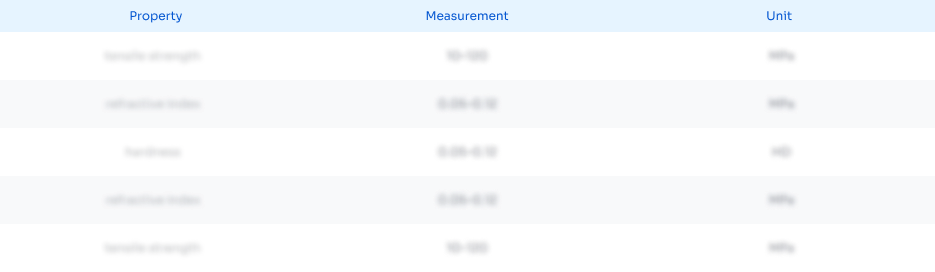
Abstract
Description
Claims
Application Information

- R&D
- Intellectual Property
- Life Sciences
- Materials
- Tech Scout
- Unparalleled Data Quality
- Higher Quality Content
- 60% Fewer Hallucinations
Browse by: Latest US Patents, China's latest patents, Technical Efficacy Thesaurus, Application Domain, Technology Topic, Popular Technical Reports.
© 2025 PatSnap. All rights reserved.Legal|Privacy policy|Modern Slavery Act Transparency Statement|Sitemap|About US| Contact US: help@patsnap.com