Core mold for manufacturing intermediate tubular shaft of coupler and manufacturing method of intermediate tubular shaft of coupler
A manufacturing method and coupling technology, which is applied in the field of mandrel and coupling intermediate tube shaft manufacturing, can solve the problem of the decrease of the torsional strength of the intermediate tube shaft, the difficulty in maintaining the coaxiality of the intermediate tube shaft, and the difficulty in processing the tapered surface, etc. problems, to improve production efficiency, avoid the decline in coaxiality, and save the effect of tapered surface processing
- Summary
- Abstract
- Description
- Claims
- Application Information
AI Technical Summary
Problems solved by technology
Method used
Image
Examples
Embodiment Construction
[0028] The present invention will be described in detail below in conjunction with the accompanying drawings.
[0029] Such as Figure 1 to Figure 4 As shown, the core mold for manufacturing the intermediate tube shaft of the coupling includes a static mold 1 and a moving mold 2, wherein the static mold 1 includes a static mold cylinder 3, which is integrally formed with the static mold cylinder 3 on the left side of the static mold cylinder 3 The static mold head 4 and the static mold shaft 5 fixedly installed in the middle of the static mold head 4, the junction of the static mold cylinder 3 and the static mold head 4 is provided with a cutting seam 12, wherein the movable mold 2 includes a dynamic The mold cylinder 6, the movable mold head 7 integrally formed with the movable mold cylinder 6 on the right side of the movable mold cylinder 6, the joint between the movable mold cylinder 6 and the movable mold head 7 is provided with two cutting seams 13. The inside of the sta...
PUM
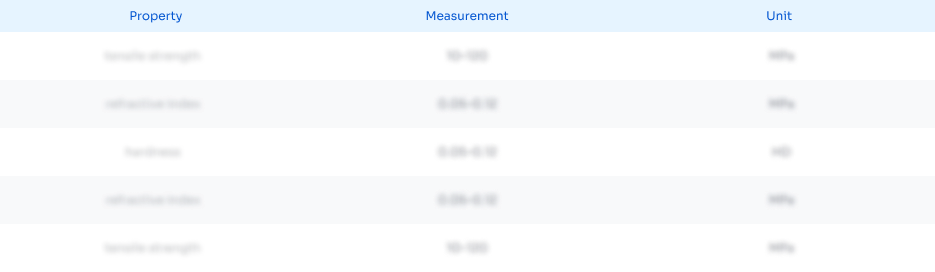
Abstract
Description
Claims
Application Information

- R&D Engineer
- R&D Manager
- IP Professional
- Industry Leading Data Capabilities
- Powerful AI technology
- Patent DNA Extraction
Browse by: Latest US Patents, China's latest patents, Technical Efficacy Thesaurus, Application Domain, Technology Topic, Popular Technical Reports.
© 2024 PatSnap. All rights reserved.Legal|Privacy policy|Modern Slavery Act Transparency Statement|Sitemap|About US| Contact US: help@patsnap.com