A method for degrading lignocellulose based on molybdenum polyoxometalates
A polyoxometalate, lignocellulose technology, applied in chemical instruments and methods, sugar production, sugar production and other directions, can solve problems such as poor cellulose degradation effect, achieve good cellulose degradation effect and simple method , the effect of high catalyst activity
- Summary
- Abstract
- Description
- Claims
- Application Information
AI Technical Summary
Problems solved by technology
Method used
Image
Examples
Embodiment 1
[0028] Example 1 1-hexyl-3-methylimidazole molybdate ([Hmim] 4 Mo 8 O 26 ) Catalytic degradation of microcrystalline cellulose
[0029] (一)1-hexyl-3-methylimidazole molybdate ([Hmim] 4 Mo 8 O 26 ) Preparation
[0030] [Hmim] 4 Mo 8 O 26 The structural formula is as follows:
[0031]
[0032] The preparation method is as follows:
[0033] 1) Add a certain amount of acetonitrile solvent to N-methylimidazole and bromo-n-hexane in a molar ratio of 1:1.2. 2 Under protection, react at 35-40°C for 1h, then heat to 70°C and reflux for 12h to obtain the reaction intermediate product [Hmim]Br. Add a mixture of acetonitrile and ethyl acetate with a volume ratio of 1:2 to recrystallize it. The crystals are washed with n-hexane for 2 to 3 times, and the pure intermediate [Hmim]Br is obtained by distillation and drying.
[0034] 2) Pass a certain amount of diluted [Hmim]Br aqueous solution through a cation resin exchange column for ion exchange, and the Br - Exchange for OH - ion. Collect the eff...
Embodiment 2
[0038] Example 2 1,2-Dimethyl-3-hexyl imidazole molybdate ([DHmim] 4 Mo 8 O 26 ) Catalytic degradation of microcrystalline cellulose
[0039] (1) 1,2-Dimethyl-3-hexylimidazole molybdate ([DHmim] 4 Mo 8 O 26 ) Preparation
[0040] [DHmim] 4 Mo 8 O 26 The structural formula is as follows:
[0041]
[0042] The preparation method is as follows:
[0043] 1) Add 1,2-dimethylimidazole and bromo-n-hexane into a certain amount of acetonitrile solvent at a molar ratio of 1:1.2, 2 Under protection, react at 35-40℃ for 1h, then heat to 70℃ and reflux for 12h to obtain the reaction intermediate product [DHmim]Br. Add a mixture of acetonitrile and ethyl acetate with a volume ratio of 1:2 to recrystallize it. The crystals are washed with n-hexane for 2 to 3 times, and the pure intermediate [DHmim]Br is obtained by distillation and drying.
[0044] 2) Pass a certain amount of diluted [DHmim]Br aqueous solution through a cation resin exchange column for ion exchange, and the Br - Exchange for OH - i...
Embodiment 3
[0048] Example 3 1-Hexylpyridine molybdate ([Hpy] 4 Mo 8 O 26 ) Catalytic degradation of microcrystalline cellulose
[0049] (1) 1-Hexyl pyridine molybdate ([Hpy] 4 Mo 8 O 26 ) Preparation
[0050] [Hpy] 4 Mo 8 O 26 The structural formula is as follows:
[0051]
[0052] The preparation method is as follows:
[0053] 1) Add pyridine and bromo-n-hexane into a certain amount of acetonitrile solvent at a molar ratio of 1:1.2. 2 Under protection, react at 35-40°C for 1h, then heat to 70°C and reflux for 12h to obtain the reaction intermediate product [Hpy]Br. Add a mixture of acetonitrile and ethyl acetate with a volume ratio of 1:2 to recrystallize it. The crystals are washed with n-hexane for 2 to 3 times, and the pure intermediate [Hpy]Br is obtained by distillation and drying.
[0054] 2) Pass a certain amount of diluted [Hpy]Br aqueous solution through a cation resin exchange column for ion exchange. - Exchange for OH - ion. Collect the effluent solution in batches and use AgNO 3 -...
PUM
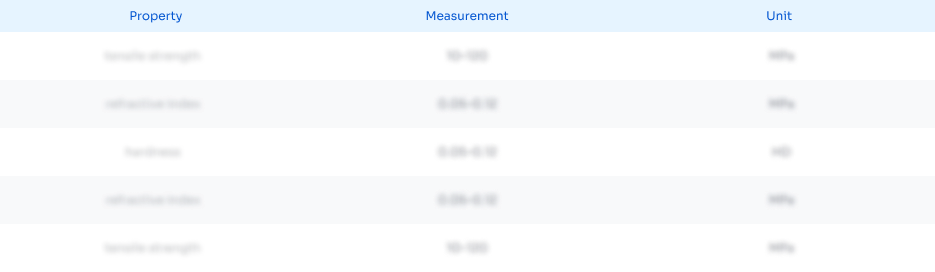
Abstract
Description
Claims
Application Information

- R&D Engineer
- R&D Manager
- IP Professional
- Industry Leading Data Capabilities
- Powerful AI technology
- Patent DNA Extraction
Browse by: Latest US Patents, China's latest patents, Technical Efficacy Thesaurus, Application Domain, Technology Topic, Popular Technical Reports.
© 2024 PatSnap. All rights reserved.Legal|Privacy policy|Modern Slavery Act Transparency Statement|Sitemap|About US| Contact US: help@patsnap.com