Metallurgical analysis etching method of layered metal composite material
A composite material, metallographic analysis technology, applied in the field of metallographic corrosion of metal materials, can solve the problem of difficult to simultaneously display the metallographic microstructure, microstructure mechanics and corrosion resistance differences and other problems
- Summary
- Abstract
- Description
- Claims
- Application Information
AI Technical Summary
Problems solved by technology
Method used
Image
Examples
Embodiment 1
[0020] Example 1: 304 stainless steel / 10# steel layered metal composite material
[0021] Sample preparation: The surface of the sample is processed by wire cutting, turning, milling, etc., then mechanically ground, and then mechanically polished until the surface is smooth and free of scratches;
[0022] Electrolytic corrosion: Place the mechanically polished sample in 10wt% chromium trioxide-ethanol solution, connect the corresponding electrodes, and perform electrolytic corrosion. During the corrosion, use 2.5V voltage, and the corrosion time is 15s. After corrosion, use water and absolute ethanol in sequence After cleaning and drying, the microstructure of the 304 stainless steel layer can be displayed;
[0023] Chemical corrosion: chemically corrode the electrolytically corroded, washed and dried samples with 4wt% nitric acid-ethanol solution for 10s, and then wash with water and absolute ethanol and dry them in turn. At this time, the 10# steel layer can be The microstr...
Embodiment 2
[0024] Example 2: 304 stainless steel / 20G steel layered metal composite material
[0025] Sample preparation: The surface of the sample is processed by wire cutting, turning, milling, etc., then mechanically ground, and then mechanically polished until the surface is smooth and free of scratches;
[0026] Electrolytic corrosion: Place the mechanically polished sample in 10wt% chromium trioxide-ethanol solution, connect the corresponding electrodes, and perform electrolytic corrosion. During the corrosion, use 2.5V voltage, and the corrosion time is 10s. After corrosion, use water and absolute ethanol in sequence After cleaning and drying, the microstructure of the 304 stainless steel layer can be displayed;
[0027] Chemical corrosion: Chemically corrode the electrolytically corroded, washed and dried samples with 8wt% nitric acid-ethanol solution for 20s. Microorganisms are shown, see figure 1 .
Embodiment 3
[0028] Example 3: 316 steel / 20G steel layered metal composite
[0029] Sample preparation: The surface of the sample is processed by wire cutting, turning, milling, etc., then mechanically ground, and then mechanically polished until the surface is smooth and free of scratches;
[0030] Electrolytic corrosion: place the mechanically polished sample in 10wt% chromium trioxide-ethanol solution, connect the corresponding electrodes, and conduct electrolytic corrosion. During the corrosion, use 3V voltage, and the corrosion time is 60s. After corrosion, clean it with water and absolute ethanol in sequence And blow dry, at this time the microstructure of the 316 stainless steel layer can be displayed;
[0031] Chemical corrosion: Chemically corrode the electrolytically corroded, washed and dried samples with 8wt% nitric acid-ethanol solution for 20s. Microtissues are revealed.
PUM
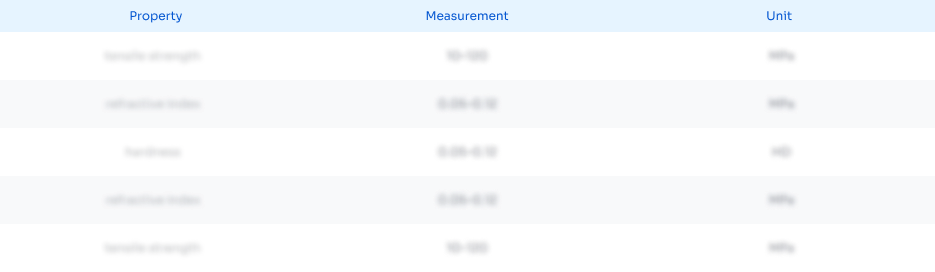
Abstract
Description
Claims
Application Information

- R&D Engineer
- R&D Manager
- IP Professional
- Industry Leading Data Capabilities
- Powerful AI technology
- Patent DNA Extraction
Browse by: Latest US Patents, China's latest patents, Technical Efficacy Thesaurus, Application Domain, Technology Topic, Popular Technical Reports.
© 2024 PatSnap. All rights reserved.Legal|Privacy policy|Modern Slavery Act Transparency Statement|Sitemap|About US| Contact US: help@patsnap.com