Synergic-purification all-heat-recovery combined heat and power generation system
A technology of combined heat and power generation and total heat recovery, applied in the energy field, can solve problems such as poor heat exchange effect, large volume, and waste of heat
- Summary
- Abstract
- Description
- Claims
- Application Information
AI Technical Summary
Problems solved by technology
Method used
Image
Examples
Embodiment 1
[0042] Such as figure 1 As shown, the air enters the air humidification device 1 and then enters the original cogeneration system after being humidified. The condensate at the bottom of the air humidification device 1 is pumped into the third gas water heating tower 2c for spraying through the water pump, and the condensate is pumped into the third air water heating tower 2c after spraying. In the air humidifier 1, the humidification function of air is realized. The spray water at the bottom of the second gas-water heating tower 2b is pumped into the spray water side of the absorption heat pump 4 through the water pump to release heat to the water side of the heating network, and then returns to the top of the second gas-water heating tower 2b for circulating spraying. The spray water at the bottom of the first gas-water heating tower 2a is pumped into the water-water heat exchanger 3 to spray the water side to release the heat to the water side of the heating network, and the...
Embodiment 2
[0046] Such as figure 2 As shown, the difference between this embodiment and Embodiment 1 is that when the secondary side of the thermal station is in the low-temperature heating mode, the thermal station only includes the conventional second water-to-water heat exchanger 9, and the second water-to-water heat exchanger The primary side inlet of 9 is connected to the water side outlet of steam-water heat exchanger 5, and the primary side low-temperature return water interface of the second water-water heat exchanger 9 is connected to the water side inlet of condenser 6 and water-water heat exchanger 3 Connection; the secondary network return water of the thermal station is connected to the secondary side low-temperature return water interface of the second water-to-water heat exchanger 9, and the secondary network water supply of the thermal station is connected to the secondary-side water supply of the second water-to-water heat exchanger 9 The interface is connected, and aft...
Embodiment 3
[0048] Such as image 3 As shown, the difference between this embodiment and Embodiment 1 is: when the secondary side of the thermal station is in the low-temperature heating mode, the thermal station includes a conventional second water-to-water heat exchanger 9 and a peak-shaving heat pump unit 8; The primary-side inlet of the second water-water heat exchanger 9 is connected to the water-side outlet of the steam-water heat exchanger 5, and the primary-side low-temperature return water interface of the second water-water heat exchanger 9 is connected to the primary side of the peak-shaving heat pump unit 8. Inlet connection, the outlet of the primary side of the peak-shaving type heat pump unit 8 is connected to the water side inlet of the condenser 6 and the water-water heat exchanger 3; The secondary side low-temperature return water interface is connected to the secondary side low-temperature return water interface of the peak-shaving heat pump unit 8; The secondary-side ...
PUM
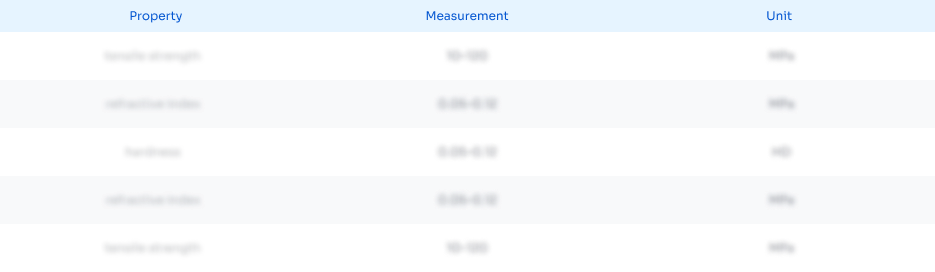
Abstract
Description
Claims
Application Information

- R&D
- Intellectual Property
- Life Sciences
- Materials
- Tech Scout
- Unparalleled Data Quality
- Higher Quality Content
- 60% Fewer Hallucinations
Browse by: Latest US Patents, China's latest patents, Technical Efficacy Thesaurus, Application Domain, Technology Topic, Popular Technical Reports.
© 2025 PatSnap. All rights reserved.Legal|Privacy policy|Modern Slavery Act Transparency Statement|Sitemap|About US| Contact US: help@patsnap.com