Method for preparing tobacco pulp from regenerated tobacco
A technology for regenerating tobacco leaves and tobacco pulp, applied in the directions of tobacco, tobacco preparation, application, etc., can solve the problems such as affecting the coating uniformity of the coating solution, poor papermaking performance and running stability, and limiting the amount of flavors and fragrances. Achieve the effect of reducing colloid aggregation and microbial deposition, increasing paper machine speed and paper yield, and increasing pulp and filler retention
- Summary
- Abstract
- Description
- Claims
- Application Information
AI Technical Summary
Problems solved by technology
Method used
Image
Examples
Embodiment 1
[0063] A method for preparing regenerated tobacco leaf tobacco pulp, comprising the following steps:
[0064] (1) Solid-liquid separation of the tobacco raw material after leaching and extraction, adding an aqueous solvent to the tobacco filter residue obtained by solid-liquid separation, and controlling the mass ratio of the filter residue to the aqueous solvent to be 1:5;
[0065] Wherein the tobacco filter residue is a mixture of tobacco stem filter residue and tobacco leaf filter residue, and the mass ratio of tobacco stem to tobacco leaf is 4:6;
[0066] the aqueous solvent comprises sodium acetate, sodium hydroxide and potassium hydroxide, and each compound is present at a concentration of 2% w / v;
[0067] The aqueous solvent also contains Tween-80 (polyoxyethylene sorbitan monooleate) at a concentration of 0.1% w / v;
[0068] Control the pH of the aqueous solvent to be 7;
[0069] (2) Send the filter residue solution into the refiner to disentangle the fibers until the...
Embodiment 2
[0075] A method for preparing regenerated tobacco leaf tobacco pulp, comprising the following steps:
[0076] (1) Solid-liquid separation of the tobacco raw material after leaching and extraction, adding a water-containing solvent to the tobacco filter residue obtained by solid-liquid separation, and controlling the mass ratio of the filter residue to the water-containing solvent to be 1:7;
[0077] Wherein the tobacco filter residue is tobacco stem filter residue;
[0078] The aqueous solvent comprises sodium acetate and sodium hydroxide, the concentration of sodium acetate is 0.1% w / v, and the concentration of sodium hydroxide is 5% w / v;
[0079] The aqueous solvent also contains op-10 (polyoxyethylene alkylphenyl ether) at a concentration of 0.04% w / v;
[0080] Controlling the pH value of the aqueous solvent is 9;
[0081] (2) sending the filter residue solution into the refiner to disentangle the fibers until the beating degree is 15°SR;
[0082] (3) Adding a compound e...
Embodiment 3
[0087] A method for preparing regenerated tobacco leaf tobacco pulp, comprising the following steps:
[0088] (1) Solid-liquid separation of the tobacco raw material after leaching and extraction, adding an aqueous solvent to the tobacco filter residue obtained by solid-liquid separation, and controlling the mass ratio of the filter residue to the aqueous solvent to be 1:4;
[0089] Wherein the tobacco filter residue is tobacco leaf filter residue;
[0090] The aqueous solvent comprises sodium acetate and potassium hydroxide, the concentration of sodium acetate is 3% w / v, and the concentration of potassium hydroxide is 0.1% w / v;
[0091] The aqueous solvent also contains AEO-9 (polyoxyethylene alkyl ether) at a concentration of 0.2% w / v;
[0092] Control the pH of the aqueous solvent to be 6;
[0093] (2) sending the filter residue solution into the refiner to disentangle the fibers until the beating degree is 15°SR;
[0094] (3) Add a compound enzyme preparation to the dec...
PUM
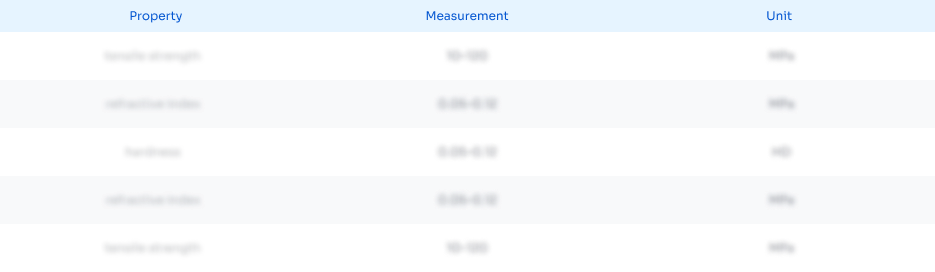
Abstract
Description
Claims
Application Information

- R&D
- Intellectual Property
- Life Sciences
- Materials
- Tech Scout
- Unparalleled Data Quality
- Higher Quality Content
- 60% Fewer Hallucinations
Browse by: Latest US Patents, China's latest patents, Technical Efficacy Thesaurus, Application Domain, Technology Topic, Popular Technical Reports.
© 2025 PatSnap. All rights reserved.Legal|Privacy policy|Modern Slavery Act Transparency Statement|Sitemap|About US| Contact US: help@patsnap.com