Production technology for indigo cotton yarn
A production process, indigo cotton technology, applied in the direction of yarn, liquid/gas/steam fiber/sliver/roving treatment, liquid/gas/steam yarn/filament treatment, etc., can solve the problem of unclear cloth surface layer, yarn Uneven color, poor color fastness of neps, etc., to achieve the effect of clear layers, natural color and less floating color
- Summary
- Abstract
- Description
- Claims
- Application Information
AI Technical Summary
Problems solved by technology
Method used
Examples
Embodiment 1
[0014] A kind of production technology of indigo cotton yarn, described preparation step comprises clearing, carding, first doubling, two dollies, three dollies, roving, spun yarn, post-processing, concrete steps are as follows:
[0015] (1) Indigo is firstly mixed with hot water, then heated up to about 90°C and added with sodium hydroxide and sodium hydrosulfite, and kept at 90°C for 3 minutes to prepare a leuco body for later use;
[0016] (2) Adjust the pH value with acetic acid, put the pretreated cotton into the indigo dyeing paint, raise the temperature to 35°C at 3°C / min, keep it warm for 30min, then raise the temperature to 120°C at 2°C / min, and continue dyeing for 20min. Then cool down to 40°C at 3°C / min, and take out the cotton;
[0017] (3) the dyed cotton is spun into cotton yarn through clearing, carding, first doubling, two doubling, three doubling, roving and spun yarn, for subsequent use;
[0018] (4) after-treatment is carried out to the cotton yarn after ab...
PUM
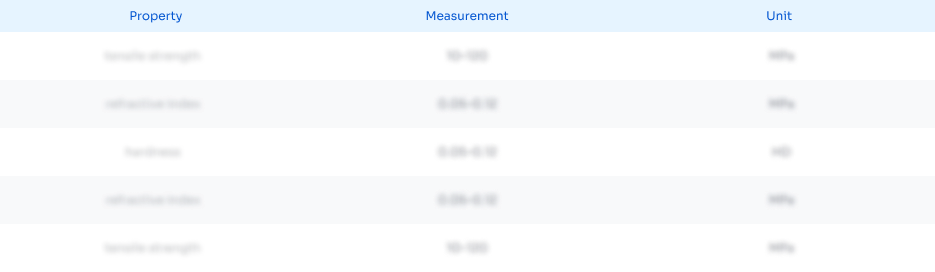
Abstract
Description
Claims
Application Information

- Generate Ideas
- Intellectual Property
- Life Sciences
- Materials
- Tech Scout
- Unparalleled Data Quality
- Higher Quality Content
- 60% Fewer Hallucinations
Browse by: Latest US Patents, China's latest patents, Technical Efficacy Thesaurus, Application Domain, Technology Topic, Popular Technical Reports.
© 2025 PatSnap. All rights reserved.Legal|Privacy policy|Modern Slavery Act Transparency Statement|Sitemap|About US| Contact US: help@patsnap.com