Magnesium alloy semi-continuous casting process
A semi-continuous casting and magnesium alloy technology, applied in the field of magnesium alloy semi-continuous casting, can solve the problems of high raw material cost and poor elastic deformation resistance, and achieve improved die-casting performance and corrosion resistance, good elastic deformation resistance, high intensity effect
- Summary
- Abstract
- Description
- Claims
- Application Information
AI Technical Summary
Problems solved by technology
Method used
Image
Examples
Embodiment 1
[0018] A magnesium alloy semi-continuous casting casting process, which includes the following steps: 1) material preparation, 2) preparation of material 1, 3) raw material preheating, 4) melting, 5) semi-continuous casting, 6) hot rolling and cold rolling, 7 )annealing.
[0019] Specifically, include the following steps:
[0020] 1) Raw material preparation: Weigh each raw material by weight for use: 1 part of neodymium, 1 part of niobium, 2 parts of zirconium, 3 parts of glass fiber, 8 parts of zinc, 10 parts of graphite, 15 parts of silicon, 20 parts of titanium, and 1000 parts of magnesium;
[0021] 2) Preparation of material 1: Add glass fiber and graphite to acetone in sequence, stir at 100 rpm for 6 hours, and then refrigerate at 4°C for 12 hours to obtain material 1; the mass ratio of acetone to graphite is 3:2 ;
[0022] 3) Raw material preheating: preheat neodymium, niobium, zirconium, zinc, silicon, titanium and magnesium at 200°C for 1 hour respectively;
[0023...
Embodiment 2
[0028] A magnesium alloy semi-continuous casting casting process, which includes the following steps: 1) material preparation, 2) preparation of material 1, 3) raw material preheating, 4) melting, 5) semi-continuous casting, 6) hot rolling and cold rolling, 7 )annealing.
[0029] Specifically, include the following steps:
[0030] 1) Raw material preparation: Weigh each raw material by weight for use: 2 parts of neodymium, 2 parts of niobium, 4 parts of zirconium, 5 parts of glass fiber, 12 parts of zinc, 15 parts of graphite, 20 parts of silicon, 30 parts of titanium, and 1300 parts of magnesium;
[0031] 2) Preparation of material 1: Add glass fiber and graphite to acetone in sequence, stir at 100 rpm for 6 hours, and then refrigerate at 4°C for 12 hours to obtain material 1; the mass ratio of acetone to graphite is 3:2 ;
[0032] 3) Raw material preheating: preheat neodymium, niobium, zirconium, zinc, silicon, titanium and magnesium at 200°C for 1 hour respectively;
[0...
Embodiment 3
[0038] The process steps are the same as in Example 1, except that graphite and glass fibers are not added.
PUM
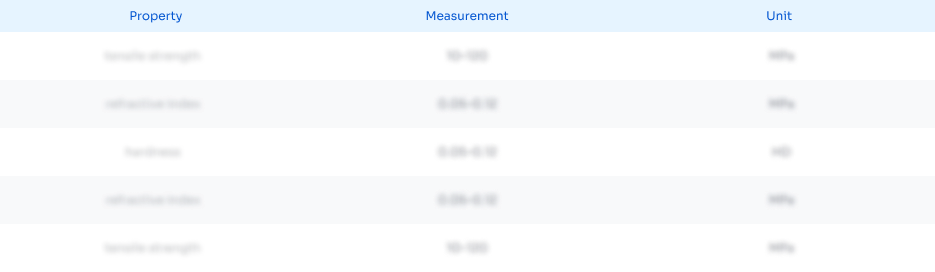
Abstract
Description
Claims
Application Information

- R&D Engineer
- R&D Manager
- IP Professional
- Industry Leading Data Capabilities
- Powerful AI technology
- Patent DNA Extraction
Browse by: Latest US Patents, China's latest patents, Technical Efficacy Thesaurus, Application Domain, Technology Topic, Popular Technical Reports.
© 2024 PatSnap. All rights reserved.Legal|Privacy policy|Modern Slavery Act Transparency Statement|Sitemap|About US| Contact US: help@patsnap.com