Preparation process of red copper square pipe material
A preparation process, the technology of red copper, applied in the direction of wire drawing die, mandrel, etc., can solve the problems of unguaranteed inner size and waist collapse, so as to achieve the effect of ensuring compliance with requirements, avoiding waist collapse, and ensuring product quality
- Summary
- Abstract
- Description
- Claims
- Application Information
AI Technical Summary
Problems solved by technology
Method used
Image
Examples
Embodiment 1
[0030] A red copper square tube, the finished product specification is 35×35×5mm, the outer dimension deviation and the inner dimension deviation are both ±0.10mm, and the radius R of the inner fillet and the outer fillet is less than or equal to 1mm. The preparation process is as follows:
[0031] Melting and casting: Put the red copper for electric conduction into coreless or cored vacuum induction furnace to melt and cast the ingot.
[0032] Ingot sawing: using a sawing machine to saw the head and tail of the ingot;
[0033] Water seal extrusion: After sawing the ingot, push the heated ingot into the extrusion barrel of a 3150-ton hydraulic press, heating temperature: 790°C, extrusion speed: 42mm / s, extrusion ratio: 21, excess thickness: 30mm, the extrusion process adopts the water seal peeling method, the ingot extruded by the extrusion shaft flows out through the outlet of the mold, and the outlet of the mold is connected to the water tank filled with water, and the extru...
Embodiment 2
[0045] A red copper square tube, the finished product specification is 25×25×4mmmm, the outer dimension deviation and the inner dimension deviation are both ±0.10mm, and the radius R of the inner fillet and the outer fillet is less than or equal to 1mm. The preparation process is as follows:
[0046] Melting and casting: Put the red copper for electric conduction into the coreless or cored vacuum induction furnace to melt and cast the ingot.
[0047] Ingot sawing: using a sawing machine to saw the head and tail of the ingot;
[0048] Water seal extrusion: After sawing the ingot, push the heated ingot into the extrusion barrel of a 3150-ton hydraulic press, heating temperature: 840°C, extrusion speed: 43mm / s, extrusion ratio: 21, excess thickness: 33mm, the extrusion process adopts the water seal peeling method, the ingot extruded by the extrusion shaft flows out through the outlet of the mold, and the outlet of the mold is connected to the water tank filled with water, and the...
Embodiment 3
[0060] A red copper square tube, the finished product specification is 45×45×6mm, the outer dimension deviation and the inner dimension deviation are both ±0.10mm, and the radius R of the inner fillet and the outer fillet is less than or equal to 1mm. The preparation process is as follows:
[0061] Melting and casting: Put the red copper for electric conduction into coreless or cored vacuum induction furnace to melt and cast the ingot.
[0062] Ingot sawing: using a sawing machine to saw the head and tail of the ingot;
[0063] Water seal extrusion: After sawing the ingot, push the heated ingot into the extrusion barrel of a 3150-ton hydraulic press, heating temperature: 830°C, extrusion speed: 42mm / s, extrusion ratio: 21, excess thickness: 33mm, the extrusion process adopts the water seal peeling method, the ingot extruded by the extrusion shaft flows out through the outlet of the mold, and the outlet of the mold is connected to the water tank filled with water, and the extru...
PUM
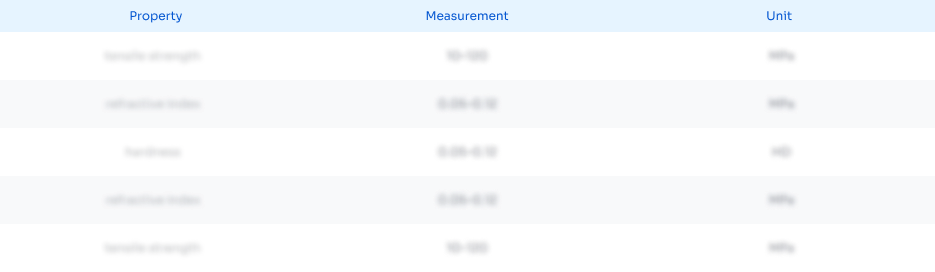
Abstract
Description
Claims
Application Information

- Generate Ideas
- Intellectual Property
- Life Sciences
- Materials
- Tech Scout
- Unparalleled Data Quality
- Higher Quality Content
- 60% Fewer Hallucinations
Browse by: Latest US Patents, China's latest patents, Technical Efficacy Thesaurus, Application Domain, Technology Topic, Popular Technical Reports.
© 2025 PatSnap. All rights reserved.Legal|Privacy policy|Modern Slavery Act Transparency Statement|Sitemap|About US| Contact US: help@patsnap.com