Semi-active vibration absorber control system based on state observation
A state observer and state observation technology, applied in the direction of shock absorber, vibration suppression adjustment, non-rotational vibration suppression, etc., can solve the problem that it is difficult to establish an accurate mathematical model, it is difficult to identify the frequency of vibration signals of rotating machinery, and it is difficult to work, etc. problems, to improve the control effect and system stability, to achieve accurate tracking, and to save costs
- Summary
- Abstract
- Description
- Claims
- Application Information
AI Technical Summary
Problems solved by technology
Method used
Image
Examples
Embodiment Construction
[0036] The composition of the semi-active vibration absorber control system based on state observation in this embodiment includes a semi-active suspension system 1 , a state observation module 2 , a phase difference cosine value calculation module 3 and a current output module 4 .
[0037] like figure 1 As shown, the semi-active suspension system 1 includes a vibration-damping object 11, a semi-active vibration absorber 12, a passive vibration isolator 13, and a sensor 14 installed on the vibration-damping object 11 or the semi-active vibration absorber 12; Perform semi-active vibration-absorbing control on the vibration of the vibration-damping object 11; use the sensor 14 to detect in real time and obtain the analog quantity of the real-time vibration signal corresponding to the output vector of the semi-active suspension system 1; the passive vibration isolator 13 is used to support the vibration-damping object 11.
[0038] The state observation module 2 comprises an anal...
PUM
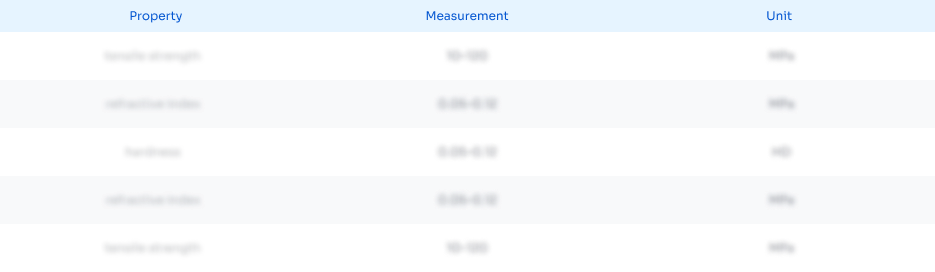
Abstract
Description
Claims
Application Information

- Generate Ideas
- Intellectual Property
- Life Sciences
- Materials
- Tech Scout
- Unparalleled Data Quality
- Higher Quality Content
- 60% Fewer Hallucinations
Browse by: Latest US Patents, China's latest patents, Technical Efficacy Thesaurus, Application Domain, Technology Topic, Popular Technical Reports.
© 2025 PatSnap. All rights reserved.Legal|Privacy policy|Modern Slavery Act Transparency Statement|Sitemap|About US| Contact US: help@patsnap.com