Preparation method of In2O3 nanoparticles/MoO3 nanorod composite materials
A technology of nanoparticles and composite materials, applied in nanotechnology, nanotechnology, analytical materials, etc.
- Summary
- Abstract
- Description
- Claims
- Application Information
AI Technical Summary
Problems solved by technology
Method used
Image
Examples
Embodiment 1
[0019] (1) A certain amount of ammonium molybdate tetrahydrate was weighed and calcined at 400°C for 3 hours to obtain molybdenum oxide powder;
[0020] (2) Weigh 6g of the prepared molybdenum oxide powder and dissolve it in 40mL of 30% hydrogen peroxide, stir to dissolve it completely, add 25mL of concentrated nitric acid and 187mL of deionized water into the above mixed solution. Stir to make the mixed solution change from a yellow suspension to a transparent and clear yellow solution;
[0021] (3) Take 35mL of the above mixed solution and transfer it to a 50mL reactor, and conduct a hydrothermal reaction at 150°C for 40h;
[0022] (4) Use a centrifuge to separate the solid-liquid product after the hydrothermal reaction, wash the solid product with deionized water and ethanol several times, place the solid product in a drying oven, and dry it at 60°C ;
[0023] (5) Weigh 0.020g of indium nitrate and dissolve it in 100mL of deionized water, and stir evenly. Weigh a certain...
Embodiment 2
[0026] (1) Weigh a certain amount of ammonium molybdate tetrahydrate and calcinate it at 500°C for 3 hours to obtain molybdenum oxide powder;
[0027] (2) Weigh 6.4g of the prepared molybdenum oxide powder and dissolve it in 50mL of 30% hydrogen peroxide, stir to dissolve it completely, add 26mL of concentrated nitric acid and 176mL of deionized water into the above mixed solution. Stir to make the mixed solution change from a yellow suspension to a transparent and clear yellow solution;
[0028] (3) Take 35mL of the above mixed solution and transfer it to a 50mL reactor, and conduct a hydrothermal reaction at 160°C for 45h;
[0029] (4) Use a centrifuge to separate the solid-liquid product after the hydrothermal reaction, wash the solid product with deionized water and ethanol several times, place the solid product in a drying oven, and dry it at 60°C ;
[0030](5) Weigh 0.022g of indium nitrate and dissolve it in 100mL of deionized water, and stir evenly. Weigh a certain ...
Embodiment 3
[0033] (1) Weigh a certain amount of ammonium molybdate tetrahydrate and calcinate it at 500°C for 4 hours to obtain molybdenum oxide powder;
[0034] (2) Weigh 6.8g of the prepared molybdenum oxide powder and dissolve it in 55mL of 30% hydrogen peroxide, stir to dissolve it completely, add 25mL of concentrated nitric acid and 172mL of deionized water into the above mixed solution. Stir to make the mixed solution change from a yellow suspension to a transparent and clear yellow solution;
[0035] (3) Take 35mL of the above mixed solution and transfer it to a 50mL reactor, and conduct a hydrothermal reaction at 170°C for 50h;
[0036] (4) Use a centrifuge to separate the solid-liquid product after the hydrothermal reaction, wash the solid product with deionized water and ethanol several times, place the solid product in a drying oven, and dry it at 60°C ;
[0037] (5) Weigh 0.024g of indium nitrate and dissolve it in 100mL of deionized water, and stir evenly. Weigh a certain...
PUM
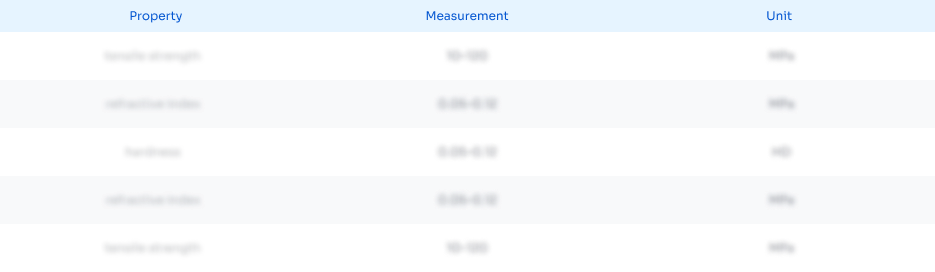
Abstract
Description
Claims
Application Information

- R&D
- Intellectual Property
- Life Sciences
- Materials
- Tech Scout
- Unparalleled Data Quality
- Higher Quality Content
- 60% Fewer Hallucinations
Browse by: Latest US Patents, China's latest patents, Technical Efficacy Thesaurus, Application Domain, Technology Topic, Popular Technical Reports.
© 2025 PatSnap. All rights reserved.Legal|Privacy policy|Modern Slavery Act Transparency Statement|Sitemap|About US| Contact US: help@patsnap.com