Automatic workpiece welding state monitoring method
A welding state, automatic monitoring technology, applied in welding equipment, auxiliary welding equipment, welding/cutting auxiliary equipment, etc., can solve the problems of difficult welding seam length, affecting welding quality, low welding strength, etc., and achieve high practical value and accuracy. Monitoring, the effect of low investment cost
- Summary
- Abstract
- Description
- Claims
- Application Information
AI Technical Summary
Problems solved by technology
Method used
Image
Examples
Embodiment Construction
[0036] Such as figure 1 A method for automatically monitoring the welding state of workpieces shown includes the following steps:
[0037] Step 1. Fix the workpiece to be welded: Fix the two workpieces 1 to be welded on the welding platform 2. For details, see figure 2 .
[0038] Step 2. Installation of electric welding frame and welding equipment: First, on the welding platform 2 described in step 1, install an electric welding machine that drives the welding equipment 3 to move from front to back along the welding area between the two workpieces 1 to be welded. frame 4, and then the welding equipment 3 is installed on the electric welding frame 4; the electric welding frame 4 is controlled by the welding controller and connected to the welding controller.
[0039] Step 3, installation of welding position detection device: install a position detection unit 5 for real-time detection of its moving position on the electric welding frame 4 installed in step 2.
[0040] Step 4...
PUM
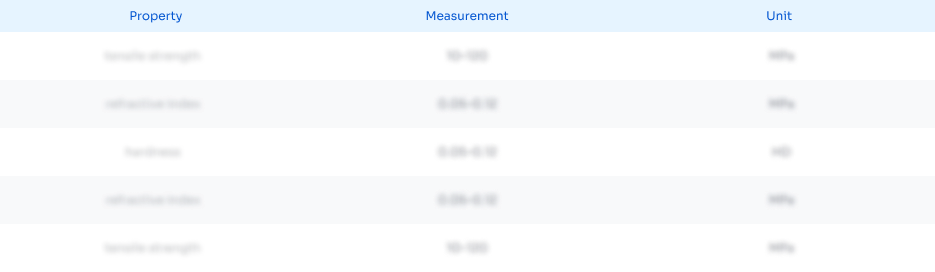
Abstract
Description
Claims
Application Information

- R&D
- Intellectual Property
- Life Sciences
- Materials
- Tech Scout
- Unparalleled Data Quality
- Higher Quality Content
- 60% Fewer Hallucinations
Browse by: Latest US Patents, China's latest patents, Technical Efficacy Thesaurus, Application Domain, Technology Topic, Popular Technical Reports.
© 2025 PatSnap. All rights reserved.Legal|Privacy policy|Modern Slavery Act Transparency Statement|Sitemap|About US| Contact US: help@patsnap.com