Method for preparing naphtha isomerization catalyst
A catalyst and isomerization technology, applied in physical/chemical process catalysts, reformed naphtha, molecular sieve catalysts, etc., can solve problems such as environmental pollution, octane number needs to be improved, and isomerization selectivity is not ideal
- Summary
- Abstract
- Description
- Claims
- Application Information
AI Technical Summary
Problems solved by technology
Method used
Image
Examples
Embodiment 1
[0026] (1) Dissolve chloroplatinic acid containing 0.3 grams of platinum in 6 grams of water, fully mix 10 grams of 200-mesh cellulose with the above solution, and dry the mixture at 80°C for 6 hours to obtain platinum-loaded cellulose.
[0027] (2) Fully knead 45 grams of mordenite, 72 grams of aluminum hydroxide dry rubber powder (SB produced by Condean, Germany, 76% on a dry basis), platinum-loaded cellulose, 50ml of 0.2M nitric acid solution and 30ml of water , making it into a paste-like plastic, forming a cylindrical strip with a diameter of 1.5mm on an extruder, drying the cylindrical strip at 110° C. for 8 hours, and then roasting at 650° C. for 4 hours in an air atmosphere to obtain a catalyst product. The pore volume of the catalyst with a pore diameter of 1-10nm accounts for 5.9% of the total pore volume, and the pore volume of 100-1000nm accounts for 55.3% of the total pore volume. The catalyst composition is shown in Table 1, and the evaluation results are shown in...
Embodiment 2~8
[0029] The same as Example 1, the difference is that the types and amounts of various substances in each step have been adjusted, and the composition of the catalyst is different. The catalyst numbers of each embodiment are E-2~E-8, and the pore-forming catalysts used in each embodiment are The dosage and catalyst composition are shown in Table 1, and the evaluation results are shown in Table 2.
Embodiment 9
[0035]E1~E8 and C1~C2 were evaluated for catalyst performance. The evaluation conditions were as follows: take hydrorefined naphtha (RON=53) as raw material, take 20ml of catalyst, dilute it with 10ml of quartz sand and fill it into a fixed-bed micro-continuous Catalytic activity evaluation was carried out in the reactor. Before the evaluation, under the conditions of pressure 2MPa and temperature 200°C, pure hydrogen was passed in at a rate of 800 gas volume ratio (the volume ratio of the entering gas to the loading volume of the catalyst), and after 2 hours, the temperature was raised to 290°C and kept The time is 4 hours for catalyst activation; then the pressure and temperature are constant, the hydrogen hydrocarbon molar ratio is adjusted to 4, and the volume space velocity is 2.0h -1 Enter the raw material, at 290°C, 2.0MPa, volume space velocity 2.0h -1 , Under the condition that the molar ratio of hydrogen to hydrocarbon is 4.0, the reaction is a constant every 8 hour...
PUM
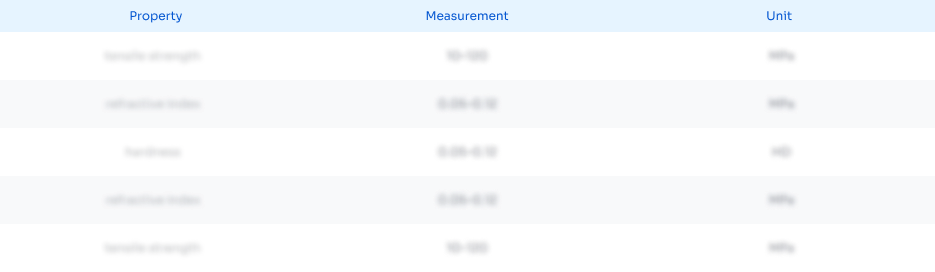
Abstract
Description
Claims
Application Information

- R&D Engineer
- R&D Manager
- IP Professional
- Industry Leading Data Capabilities
- Powerful AI technology
- Patent DNA Extraction
Browse by: Latest US Patents, China's latest patents, Technical Efficacy Thesaurus, Application Domain, Technology Topic, Popular Technical Reports.
© 2024 PatSnap. All rights reserved.Legal|Privacy policy|Modern Slavery Act Transparency Statement|Sitemap|About US| Contact US: help@patsnap.com