Fluid catalytic cracking method of shale oil
A fluid catalytic cracking and catalytic cracking technology, which is applied in the field of efficient utilization of shale oil resources, can solve the problems of high content and low conversion efficiency, and achieve the effects of high volume utilization, high conversion rate and short process
- Summary
- Abstract
- Description
- Claims
- Application Information
AI Technical Summary
Problems solved by technology
Method used
Image
Examples
Embodiment 1
[0082] according to figure 1 The flow of the experiment was carried out, and the shale oil A in Table 1 was used as the raw material for catalytic cracking, and the experiment was carried out on a composite reactor composed of a fluidized bed and a riser. The shale oil A was fed from the bottom, and the bottom of the reactor was fluidized. The diameter of the bed expands into an adsorption zone, and a cold regenerant (the first catalytic cracking catalyst) that takes heat from outside is introduced, while the lower part of the riser reactor is transported into a high-temperature hot regenerant (the second catalytic cracking catalyst), and in the riser reactor , The upper part forms a cracking zone; the CAT-3 catalyst in Table 2 is used, and the heavy oil refining ratio is 0.1. After being preheated at 350°C, shale oil A enters the bottom of the adsorption zone where the diameter of the reactor expands (the inner diameter of the adsorption zone is 3 times the inner diameter of ...
Embodiment 2
[0085] Carry out catalytic cracking according to the method identical with embodiment 1, difference is: introduce the fresh catalyst that exchanges heat with heat regenerative catalytic cracking catalyst as the first catalytic cracking catalyst in the adsorption zone of reactor bottom, operating conditions and product distribution are listed in Table 3.
Embodiment 3
[0093] This example follows figure 2 The process is tested, using shale oil A in Table 1 as the raw material for catalytic cracking, in such as figure 2 The test is carried out on the shown reactor, the shale oil A is fed under, and the diameter of the fluidized bed at the bottom of the reactor is enlarged to be an adsorption zone (the inner diameter of the adsorption zone is 3 times the inner diameter of the cracking zone, and the length of the adsorption zone is 35% of the length of the cracking zone), and introduce a cold regenerant that takes heat from outside, while the lower part of the riser reactor is transported into a high-temperature hot regenerant to form a cracking zone in the upper part of the reactor; using CAT-3 catalyst, the heavy oil is recycled The refining ratio is 0.1. After being preheated at 350°C, shale oil A enters the bottom of the reactor's expanded fluidized bed adsorption zone, and flows upwards with a proper amount of water vapor as the fluidiz...
PUM
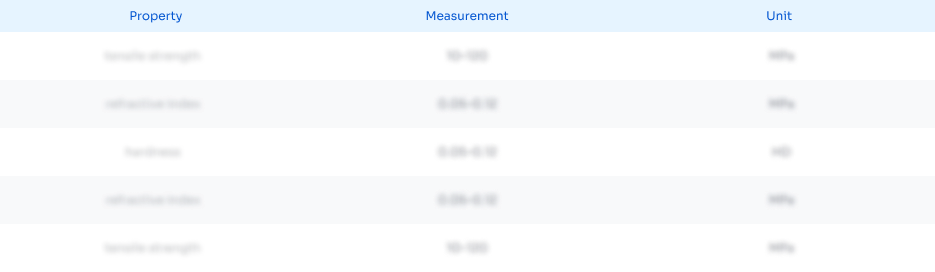
Abstract
Description
Claims
Application Information

- R&D
- Intellectual Property
- Life Sciences
- Materials
- Tech Scout
- Unparalleled Data Quality
- Higher Quality Content
- 60% Fewer Hallucinations
Browse by: Latest US Patents, China's latest patents, Technical Efficacy Thesaurus, Application Domain, Technology Topic, Popular Technical Reports.
© 2025 PatSnap. All rights reserved.Legal|Privacy policy|Modern Slavery Act Transparency Statement|Sitemap|About US| Contact US: help@patsnap.com