Machining technology for improving fatigue damage resisting performance of 2xxx aluminum alloy plate
A technology of anti-fatigue damage, aluminum alloy plate, applied in the field of non-ferrous metal material engineering, to achieve a wide range of applications
- Summary
- Abstract
- Description
- Claims
- Application Information
AI Technical Summary
Problems solved by technology
Method used
Image
Examples
Embodiment 1
[0036] According to the element ratio of 4.32wt.% Cu, 1.35wt.% Mg, 0.61wt.% Mn, 0.08wt.% Fe, 0.06wt.% Si, 0.03wt.% Ti, the 2524 aluminum alloy with a size of 400×1620×2500mm was cast Ingot. The alloy ingot is subjected to 498°C / 32h homogenization treatment, face milling, aluminum cladding, 480°C / 8h preheating, and then hot rough rolling at 480°C, followed by hot finish rolling to 6.0mm, and then recrystallization pre-annealing For treatment, the hot finish-rolled sheet is heated to 350°C at an average rate of 36°C / h or 9h to 350°C, and then kept at a temperature of 4h, followed by solution quenching at 496°C / 50min, straightening treatment and natural aging for more than 96h, process such as figure 1 shown. Test the tensile mechanical properties of the final finished plate, and test the fatigue crack growth rate of the plate according to GB / T6398-2000 and AMS4296 standards.
Embodiment 2
[0038] According to the element ratio of 4.32wt.% Cu, 1.35wt.% Mg, 0.61wt.% Mn, 0.08wt.% Fe, 0.06wt.% Si, 0.03wt.% Ti, the 2524 aluminum alloy with a size of 400×1620×2500mm was cast Ingot. The ingot was subjected to 498°C / 32h homogenization treatment, face milling, aluminum cladding, 480°C / 8h preheating, and then hot rough rolling at 480°C, followed by hot finish rolling to 6.0mm. The hot finish rolling plate is deformed to 2.5mm by cold final rolling at a reduction rate of 58%, and then recrystallized and pre-annealed, and the temperature is raised to 340°C at an average rate of 63°C / h or 5h to 340°C, and kept for 4h , and then through 496 ℃ / 25min solution quenching, and after straightening treatment, natural aging for more than 96h, the process flow is as follows figure 2 shown. Test the mechanical properties of the final finished plate, and test the fatigue crack growth rate of the plate according to GB / T6398-2000 and AMS4296 standards.
Embodiment 3
[0040] According to the element ratio of 4.32wt.% Cu, 1.35wt.% Mg, 0.61wt.% Mn, 0.08wt.% Fe, 0.06wt.% Si, 0.03wt.% Ti, the 2524 aluminum alloy with a size of 400×1620×2500mm was cast Ingot. The ingot was subjected to 498°C / 32h homogenization treatment, face milling, aluminum cladding, 480°C / 8h preheating, and then hot rough rolling at 480°C, followed by hot finish rolling to 6.0mm. The hot finish rolling plate is deformed to 2.5mm by cold final rolling at a reduction rate of 58%, and then recrystallized and pre-annealed, and the temperature is raised to 340°C at an average rate of 150°C / h or to 340°C after 2.1h, and kept 4h, and then 496℃ / 25min solution quenching, and after straightening treatment, natural aging for more than 96h, the process flow is as follows figure 2 shown. Test the mechanical properties of the final finished plate, and test the fatigue crack growth rate of the plate according to GB / T6398-2000 and AMS4296 standards.
PUM
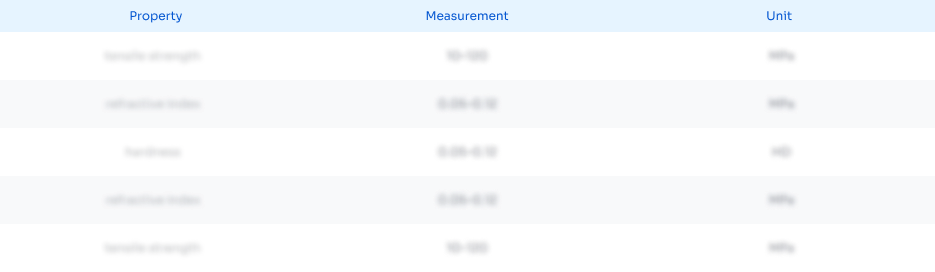
Abstract
Description
Claims
Application Information

- Generate Ideas
- Intellectual Property
- Life Sciences
- Materials
- Tech Scout
- Unparalleled Data Quality
- Higher Quality Content
- 60% Fewer Hallucinations
Browse by: Latest US Patents, China's latest patents, Technical Efficacy Thesaurus, Application Domain, Technology Topic, Popular Technical Reports.
© 2025 PatSnap. All rights reserved.Legal|Privacy policy|Modern Slavery Act Transparency Statement|Sitemap|About US| Contact US: help@patsnap.com