Buckwheat husking technology
A technology, buckwheat technology, applied in the field of buckwheat husking technology, can solve the problem of low secondary husking rate, achieve remarkable effect, promote loosening, and increase the effect of color difference
- Summary
- Abstract
- Description
- Claims
- Application Information
AI Technical Summary
Problems solved by technology
Method used
Image
Examples
Embodiment 1
[0037] A buckwheat shelling process, comprising the steps of:
[0038] 1) Screening: the mixture containing a small part of buckwheat husk, buckwheat and shelled buckwheat after husking is first screened through a vibrating grading sieve A with upper and lower screens, and the first paddy separation is carried out, and the buckwheat husk is The suction-type vertical suction separator is sent to the collection bin of the air net system; the upper sieve of the sieve body is large-grain hulled buckwheat, accounting for 14% of the mass of the hulled buckwheat in the mixture; the lower sieve The under-sieve is broken buckwheat and dust, and enters the collection bin; the sieve on the lower sieve is buckwheat and small-grain shelled buckwheat, wherein the mass ratio of buckwheat is 48%;
[0039] Described mixed material is the mixed material after buckwheat husking rate is 43% after shelling;
[0040] The vibrating grading screen A upper screen and the lower screen are square hole ...
Embodiment 2
[0059] A buckwheat shelling process, comprising the steps of:
[0060] 1) Screening: the mixture containing a small part of buckwheat husk, buckwheat and shelled buckwheat after husking is first screened through a vibrating grading sieve A with upper and lower screens, and the first paddy separation is carried out, and the buckwheat husk is The suction-type vertical suction separator is sent to the collection bin of the air net system; the upper sieve of the sieve body is large-grain shell buckwheat, accounting for 12% of the mass of shell buckwheat in the mixture; the lower sieve The under-sieve is broken buckwheat and dust, and enters the collection bin; the sieve on the lower sieve is buckwheat and small-grain shelled buckwheat, wherein the mass ratio of buckwheat is 46%;
[0061] Described mixed material is the mixed material after buckwheat husking rate is 42% after shelling;
[0062] The vibrating grading screen A upper screen and the lower screen are square hole screen...
Embodiment 3
[0081] A buckwheat shelling process, comprising the steps of:
[0082] 1) Screening: the mixture containing a small part of buckwheat husk, buckwheat and shelled buckwheat after husking is first screened through a vibrating grading sieve A with upper and lower screens, and the first paddy separation is carried out, and the buckwheat husk is The suction-type vertical suction separator is sent to the collection bin of the air net system; the upper sieve of the sieve body is large-grain hulled buckwheat, accounting for 15% of the mass of the hulled buckwheat in the mixture; the lower sieve The under-sieve is broken buckwheat and dust, which enters the collection bin; the over-sieve of the lower sieve is buckwheat and small-grain shelled buckwheat, wherein the mass ratio of buckwheat is 50%;
[0083] Described mixed material is the mixed material after buckwheat husking rate is 44% after shelling;
[0084] The vibrating grading screen A upper screen and the lower screen are squar...
PUM
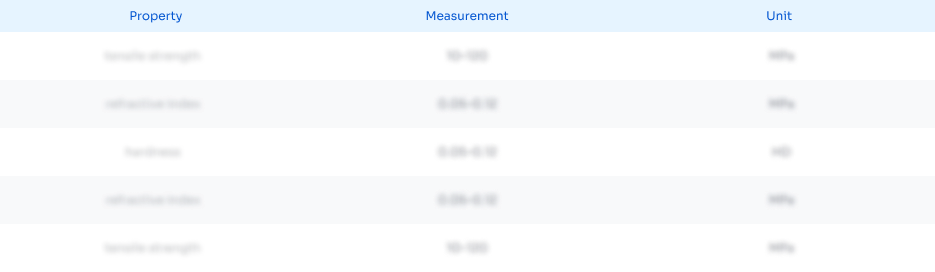
Abstract
Description
Claims
Application Information

- R&D
- Intellectual Property
- Life Sciences
- Materials
- Tech Scout
- Unparalleled Data Quality
- Higher Quality Content
- 60% Fewer Hallucinations
Browse by: Latest US Patents, China's latest patents, Technical Efficacy Thesaurus, Application Domain, Technology Topic, Popular Technical Reports.
© 2025 PatSnap. All rights reserved.Legal|Privacy policy|Modern Slavery Act Transparency Statement|Sitemap|About US| Contact US: help@patsnap.com