Functionalized boron nitride nanosheet/polypropylene composite material and preparation method thereof
A composite material and boron nitride technology, applied in the field of functionalized boron nitride nanosheet/polypropylene composite material and its preparation, can solve the problems of affecting the filling and dispersing effect of BN nanosheets, easy agglomeration and high surface energy, and achieve improvement Mechanical strength, avoid aging, improve the effect of mechanical properties
- Summary
- Abstract
- Description
- Claims
- Application Information
AI Technical Summary
Problems solved by technology
Method used
Image
Examples
Embodiment A
[0014] The weight percentage of each component is: 70 parts of homopolymerized or copolymerized polypropylene, 0 parts of functionalized boron nitride nanosheet BN-LCP, 15 parts of alkali-free glass fiber yarn, 5 parts of grafted PP, 10 parts of barium sulfate, and 0.15 parts of antioxidant parts, 0.3 parts of other additives; the materials according to the above weight percentages are added to a high-speed mixer and mixed evenly; the mixed materials enter the extruder, and are extruded by a twin-screw extruder with a melting temperature of 180-230 ° C. After cooling, cutting Granulation, sieving, and packaging to obtain unmodified polypropylene composite material A.
Embodiment B
[0016] The weight percentage of each component is: 65 parts of homopolymerized or copolymerized polypropylene, 5 parts of functionalized boron nitride nanosheet BN-LCP, 15 parts of alkali-free glass fiber yarn, 5 parts of grafted PP, 10 parts of barium sulfate, and 0.15 parts of antioxidant parts, 0.3 parts of other additives; the materials according to the above weight percentages are added to a high-speed mixer and mixed evenly; the mixed materials enter the extruder, and are extruded by a twin-screw extruder with a melting temperature of 180-230 ° C. After cooling, cutting Granulation, sieving, and packaging to obtain the functionalized boron nitride nanosheet / polypropylene composite material B.
Embodiment C
[0018] The weight percentage of each component is: 60 parts of homopolymerized or copolymerized polypropylene, 10 parts of functionalized boron nitride nanosheet BN-LCP, 15 parts of alkali-free glass fiber yarn, 5 parts of grafted PP, 10 parts of barium sulfate, and 0.15 parts of antioxidant parts, 0.3 parts of other additives; the materials according to the above weight percentages are added to a high-speed mixer and mixed evenly; the mixed materials enter the extruder, and are extruded by a twin-screw extruder with a melting temperature of 180-230 ° C. After cooling, cutting Granulation, sieving, and packaging to obtain functionalized boron nitride nanosheet / polypropylene composite material C.
PUM
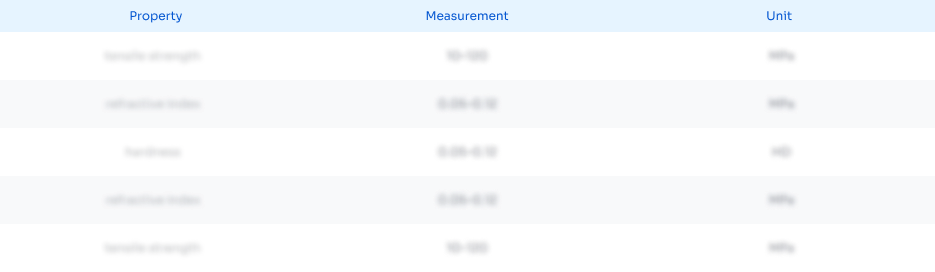
Abstract
Description
Claims
Application Information

- Generate Ideas
- Intellectual Property
- Life Sciences
- Materials
- Tech Scout
- Unparalleled Data Quality
- Higher Quality Content
- 60% Fewer Hallucinations
Browse by: Latest US Patents, China's latest patents, Technical Efficacy Thesaurus, Application Domain, Technology Topic, Popular Technical Reports.
© 2025 PatSnap. All rights reserved.Legal|Privacy policy|Modern Slavery Act Transparency Statement|Sitemap|About US| Contact US: help@patsnap.com