A Method for Controlling Full Position Trajectory of Pipeline Butt Weld
A technology of butt weld and trajectory control, applied in manufacturing tools, welding equipment, arc welding equipment, etc., can solve the problems of unable to use swing arc tracking, unable to meet welding trajectory control, low welding seam tracking accuracy, etc., to improve welding. The degree of automation, shielding the interference of the current discrete value to the compensation value, and the effect of the accurate compensation value
- Summary
- Abstract
- Description
- Claims
- Application Information
AI Technical Summary
Problems solved by technology
Method used
Image
Examples
Embodiment Construction
[0035] The embodiment of the present application provides a method for controlling the full position trajectory of the pipe butt weld, which solves or partially solves the problem that the welding trajectory control method in the prior art cannot use swing arc tracking in root welding and cover welding, and cannot meet the full position. The requirements of position welding trajectory control, the technical problems of low welding seam tracking accuracy and poor anti-interference ability in the welding process, by combining the teaching and reproduction method of industrial robots with the swing arc tracking method, the two complement each other , realize the automatic control of the welding trajectory of the pipe butt weld from root welding, filling welding to cover welding, effectively improve the automation degree of pipeline welding, effectively shield the interference of current discrete value on compensation value, and improve the accuracy of welding torch sway compensatio...
PUM
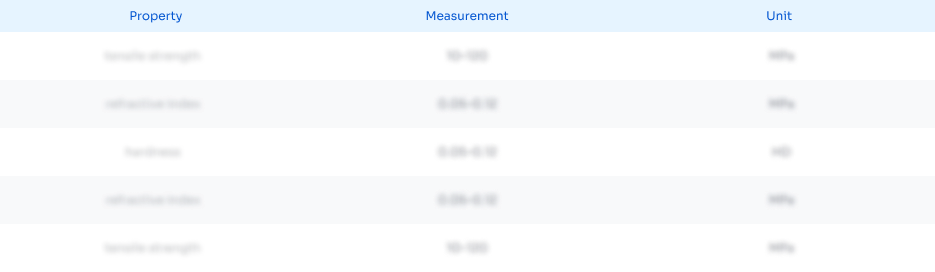
Abstract
Description
Claims
Application Information

- R&D
- Intellectual Property
- Life Sciences
- Materials
- Tech Scout
- Unparalleled Data Quality
- Higher Quality Content
- 60% Fewer Hallucinations
Browse by: Latest US Patents, China's latest patents, Technical Efficacy Thesaurus, Application Domain, Technology Topic, Popular Technical Reports.
© 2025 PatSnap. All rights reserved.Legal|Privacy policy|Modern Slavery Act Transparency Statement|Sitemap|About US| Contact US: help@patsnap.com