Method for three-dimensional reconstruction of defected part of tip of aeroengine compressor blade
An aero-engine and three-dimensional reconstruction technology, which is applied in the field of machine vision, can solve the problems of a long time consumption, a rapid reconstruction method of a three-dimensional model of a missing part of a blade tip of an aero-engine compressor blade, and a limited scope of application.
- Summary
- Abstract
- Description
- Claims
- Application Information
AI Technical Summary
Problems solved by technology
Method used
Image
Examples
Embodiment Construction
[0026] The present invention will be further described in detail below in conjunction with the embodiments and accompanying drawings. The examples are only used to further describe the present invention in detail, and do not limit the protection scope of the claims of the present application.
[0027] Aeroengine compressor blade tip (abbreviation blade) defect position three-dimensional model (abbreviation three-dimensional) reconstruction method (abbreviation or method, see for short) of the present invention design Figure 1-8 ) is as follows, after detection, the maximum distance between the blade defect vertex and the defect plane is 4.35mm, and the steps of the reconstruction method are as follows:
[0028] 1) Blade pretreatment and clamping; pick out repairable blade tip defects, and remove the oxide layer on the blade tip surface by machining; then stably clamp the machined blades with fixed fixtures, and require parallel to the horizontal plane;
[0029] 2) image acq...
PUM
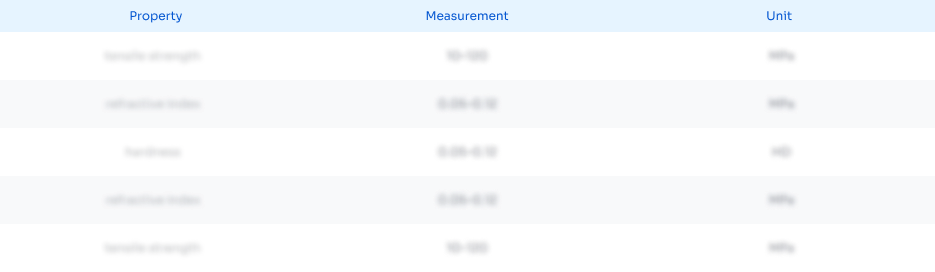
Abstract
Description
Claims
Application Information

- R&D Engineer
- R&D Manager
- IP Professional
- Industry Leading Data Capabilities
- Powerful AI technology
- Patent DNA Extraction
Browse by: Latest US Patents, China's latest patents, Technical Efficacy Thesaurus, Application Domain, Technology Topic, Popular Technical Reports.
© 2024 PatSnap. All rights reserved.Legal|Privacy policy|Modern Slavery Act Transparency Statement|Sitemap|About US| Contact US: help@patsnap.com