Coil manufacturing method, chip component and manufacturing method thereof
A manufacturing method and coil technology, which can be used in coil manufacturing, electrical components, transformer/inductor coils/windings/connections, etc., can solve the problems of electrical conductivity failing to meet predetermined requirements and poor compactness.
- Summary
- Abstract
- Description
- Claims
- Application Information
AI Technical Summary
Problems solved by technology
Method used
Image
Examples
Embodiment 1
[0057] A coil manufacturing method, used for the preparation of internal electrode coils in electronic components, the electrode pattern of the internal electrode coils of the electronic components is generated by pressing and etching copper foil, such as figure 1 shown, including the following steps:
[0058]S1: Preparation of internal electrode green sheets: slurry preparation and green sheet molding. The slurry is prepared by adding iron-based alloy materials and PVB organic solvents together for 24 hours of ball milling and mixing. The green sheets are produced by casting. , here the scraper method is used to make the green sheet;
[0059] S2: Copper foil pressing: select copper foil of predetermined thickness and cover it on the green sheet. In this embodiment, the hot water isostatic pressing method is used to press the copper foil on the green sheet to ensure that the It is firmly connected with the green sheet, and the pressure of the hot water isostatic pressing is b...
Embodiment 2
[0065] A chip component such as Figure 2-4 As shown, it includes an integrated sintered magnet 1, an inner electrode coil 2 and an outer electrode 3; the magnet 1 is made of an iron-based alloy material; the inner electrode coil 2 includes an electrode layer body and is pressed onto the electrode layer Copper foil on the body; the outer electrode 3 is arranged outside the magnet 1 and connected to the inner electrode coil 2; the inner electrode coil 2 includes an upper electrode 21, a lower electrode 23 and a and the stacked body 22 between the lower electrode 23 , the upper electrode 21 and the lower electrode 23 are respectively electrically connected to the stacked body 22 through connection points.
[0066] The connection point includes a through hole 24 penetrating through the electrode layer body, and a copper connecting body disposed in the through hole 24, and the copper connecting body is connected to the electrode pattern on the electrode layer body.
[0067] The s...
Embodiment 3
[0069] A method for manufacturing a chip component, used to make the chip component described in the second embodiment above, such as Figure 5 shown, including the following steps:
[0070] Production of the inner electrode coil: adopt the coil production method of the first embodiment above;
[0071] Making connection points: opening holes on the green sheet, filling the holes with copper paste by printing process to form connection points; the solid content of the copper paste filling is above 90wt%, and the copper paste volume shrinkage rate is less than 2%.
[0072] Lamination pressing: the electrode layers are electrically connected through connection points to form a stack, the upper electrode and the lower electrode are respectively electrically connected to the stack through connection points, and the upper electrode, the lower electrode and the stack The body is pressed into a whole to form a laminated body;
PUM
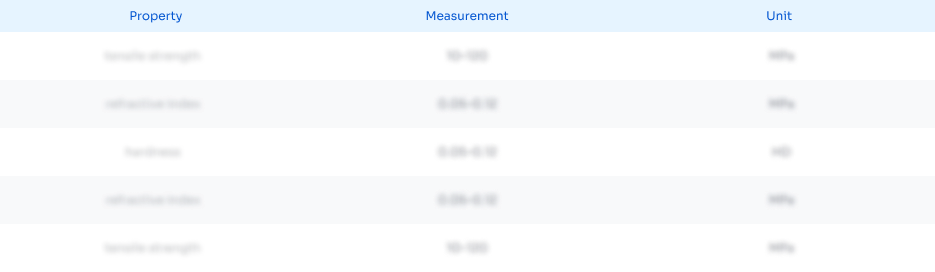
Abstract
Description
Claims
Application Information

- R&D Engineer
- R&D Manager
- IP Professional
- Industry Leading Data Capabilities
- Powerful AI technology
- Patent DNA Extraction
Browse by: Latest US Patents, China's latest patents, Technical Efficacy Thesaurus, Application Domain, Technology Topic, Popular Technical Reports.
© 2024 PatSnap. All rights reserved.Legal|Privacy policy|Modern Slavery Act Transparency Statement|Sitemap|About US| Contact US: help@patsnap.com