Filling masterbatch and preparation method thereof
A technology of filling masterbatches and inorganic powders, which is applied in the field of filling masterbatches and its preparation, can solve the problems of increasing attenuation of mechanical properties of products, and achieve the effects of low cost, large output and high mechanical strength
- Summary
- Abstract
- Description
- Claims
- Application Information
AI Technical Summary
Problems solved by technology
Method used
Examples
preparation example Construction
[0027] The present invention also provides a kind of preparation method of above-mentioned filler masterbatch, specifically comprises the following steps:
[0028] Step 1: Put the inorganic powder, dispersant and coupling agent into the powder coating machine at the same time according to the weight percentage requirements for coating modification. The modification temperature is 90-130 ° C and the time is 5-15 minutes to obtain coating Modified inorganic powder;
[0029] Step 2: Put the coated and modified inorganic powder obtained in step 1 together with the carrier resin, lubricant, and antioxidant into the internal mixer for banbury mixing. The temperature for banbury mixing is 90-150°C. The time is 10-30min, and the mixed material is obtained;
[0030] Step 3: Put the mixed material mixed in Step 2 into a granulator to extrude and granulate, and then screen and package to obtain the filled masterbatch.
Embodiment 1
[0032] This embodiment provides a filling masterbatch, which specifically includes the following components by weight: 70% of inorganic powder, 4% of coupling agent, 3% of dispersant, 20% of carrier resin, 2% of lubricant and 1% antioxidants.
[0033] This embodiment also provides a method for preparing the above-mentioned filler masterbatch, which specifically includes the following process:
[0034] Step 1: Put 70% by weight of 70% inorganic powder, 4% coupling agent, and 3% dispersant into a powder coating machine for coating modification at a temperature of 100°C for 10 minutes;
[0035] Step 2: Put the coated and modified inorganic powder, 20% by weight of carrier resin, 2% of lubricant 2%, and 1% of antioxidant into an internal mixer for internal mixing and mixing at a temperature of 115 ℃, the time is 25min;
[0036] Step 3: Put the mixed material into the granulator, extrude and granulate, screen and pack, and then get the filled masterbatch.
Embodiment 2
[0038] This embodiment provides a filling masterbatch, which specifically includes the following ingredients in weight percentage: 75% of inorganic powder, 5% of coupling agent, 2% of dispersant, 15% of carrier resin, 2.5% of lubricant and 0.5% Antioxidant.
[0039] This embodiment also provides a preparation method for filling master batches, which specifically includes the following steps:
[0040] Step 1: Put 75% by weight of inorganic powder, 5% of coupling agent, and 2% of dispersant into the powder coating machine for coating modification, the temperature is 110 ° C, and the time is 15 minutes;
[0041] Step 2: Put the coated and modified inorganic powder, 15% by weight carrier resin, 2.5% lubricant and 0.5% antioxidant into an internal mixer for internal mixing at a temperature of 115°C. The time is 20 minutes;
[0042] Step 3: Put the mixed material into the granulator, extrude and granulate, screen and pack, and then get the filled masterbatch.
PUM
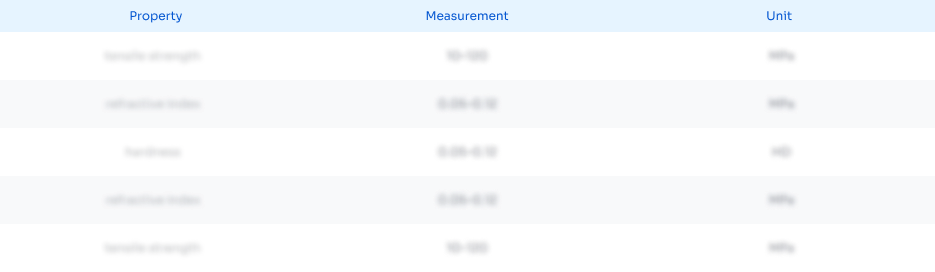
Abstract
Description
Claims
Application Information

- R&D
- Intellectual Property
- Life Sciences
- Materials
- Tech Scout
- Unparalleled Data Quality
- Higher Quality Content
- 60% Fewer Hallucinations
Browse by: Latest US Patents, China's latest patents, Technical Efficacy Thesaurus, Application Domain, Technology Topic, Popular Technical Reports.
© 2025 PatSnap. All rights reserved.Legal|Privacy policy|Modern Slavery Act Transparency Statement|Sitemap|About US| Contact US: help@patsnap.com