Manufacturing method of cooler
A manufacturing method and radiator technology, applied in heat exchange equipment and other directions, can solve the problems of unsatisfactory heat dissipation effect, long heat dissipation path of heat sink, short service life of heat source, etc., to achieve rapid conduction and dissipation, shorten heat dissipation path, and prolong use. effect of life
- Summary
- Abstract
- Description
- Claims
- Application Information
AI Technical Summary
Problems solved by technology
Method used
Image
Examples
Embodiment Construction
[0023] Such as Figure 1-Figure 3 Shown, the manufacturing method of radiator of the present invention, comprises the following steps:
[0024] Firstly, pre-press a pole of the U-shaped heat pipe 1 so that a boss 11 is formed on the pole;
[0025] Then, the heat dissipation fins 2 are sleeved one by one on the other support rod of the U-shaped heat pipe 1 through the connecting holes 21 provided thereon, and are respectively fixed by riveting with the support rod, and each heat dissipation fin fixed by riveting is The fins 2 jointly form a heat dissipation fin group, and a groove 22 and a connecting groove 24 are formed on the surface of the heat dissipation fin group, and a snap groove 23 is formed in the groove 22, and the U-shaped heat pipe 1 is provided with a convex The pole of platform 11 is placed in connecting groove 24 and boss 11 is positioned at the position of groove 22; Wherein, as image 3 As shown, the groove 22 is a square groove, and the square groove is for...
PUM
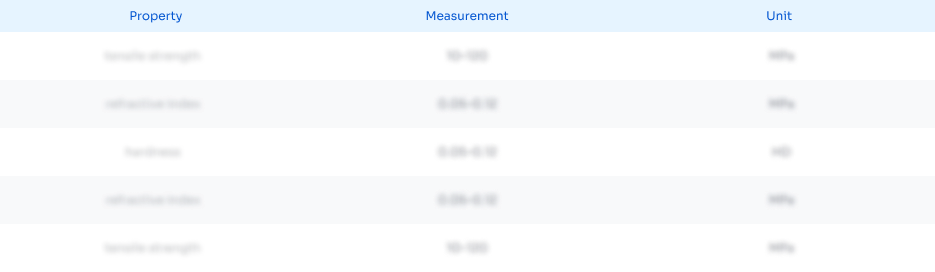
Abstract
Description
Claims
Application Information

- R&D
- Intellectual Property
- Life Sciences
- Materials
- Tech Scout
- Unparalleled Data Quality
- Higher Quality Content
- 60% Fewer Hallucinations
Browse by: Latest US Patents, China's latest patents, Technical Efficacy Thesaurus, Application Domain, Technology Topic, Popular Technical Reports.
© 2025 PatSnap. All rights reserved.Legal|Privacy policy|Modern Slavery Act Transparency Statement|Sitemap|About US| Contact US: help@patsnap.com