SLM (Selective Laser Melting) process based part lightweight design processing method
A technology of lightweight design and processing methods, applied in computing, image data processing, special data processing applications, etc., can solve problems such as difficult removal of support structures and structures that cannot be processed by SLM technology, and achieve the effect of simplifying the design process
- Summary
- Abstract
- Description
- Claims
- Application Information
AI Technical Summary
Problems solved by technology
Method used
Image
Examples
Embodiment Construction
[0015] Such as figure 1 As shown, the light-weight design and processing method for parts based on the SLM process in this embodiment includes the following steps: establishing a finite element model through a three-dimensional digital model of the part, defining loads and boundary conditions; performing topology optimization of the part to generate an initial lightweight model, and The mechanical properties of the initial lightweight model are analyzed, and self-supporting porous structures of different densities are arranged according to the stress distribution of the initial lightweight model to generate a final lightweight model; the resulting final lightweight model is processed by selective laser melting forming technology The final lightweight solid part, the topology optimization model of this embodiment is:
[0016] findX=(x 1 , x 2 ,K,x n );
[0017]
[0018] s.t.KU=F(1);
[0019]
[0020] 0i ≤1, i=1, K, n
[0021] Among them, X is the design variable; n ...
PUM
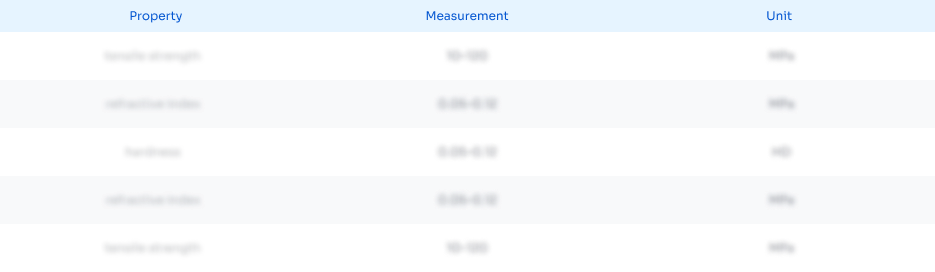
Abstract
Description
Claims
Application Information

- R&D
- Intellectual Property
- Life Sciences
- Materials
- Tech Scout
- Unparalleled Data Quality
- Higher Quality Content
- 60% Fewer Hallucinations
Browse by: Latest US Patents, China's latest patents, Technical Efficacy Thesaurus, Application Domain, Technology Topic, Popular Technical Reports.
© 2025 PatSnap. All rights reserved.Legal|Privacy policy|Modern Slavery Act Transparency Statement|Sitemap|About US| Contact US: help@patsnap.com