Method for producing trifluoroethylene
A technology of trifluoroethylene and a manufacturing method, which is applied in chemical instruments and methods, halogenated hydrocarbon preparation, halogenated hydrocarbon disproportionation preparation, etc., can solve the problems of increased amount of by-products, long reaction time, blockage of polymer by-products, etc. Achieve the effect of reducing cost and small greenhouse effect coefficient
- Summary
- Abstract
- Description
- Claims
- Application Information
AI Technical Summary
Problems solved by technology
Method used
Image
Examples
example 1
[0079] use figure 1 In the reaction apparatus shown, crude HFO-1123 was obtained by reacting as follows from a raw material gas composed of R31, R22, and TFE.
[0080] R31 was continuously introduced into a stainless steel tube preheater 2a in an electric furnace set at a furnace temperature of 300°C, and R31 was preheated to 300°C. In addition, R22 was continuously introduced into a preheater 3a made of stainless steel tubes in an electric furnace set at 300°C to preheat R22 to 300°C. Then, TFE was continuously introduced into a preheater 4a made of stainless steel tube in an electric furnace whose temperature was set at 300°C, and TFE was preheated to 300°C.
[0081] The steam (steam) heated by the heating steam generator 5a which is an electric furnace whose inner temperature is set to 850°C was supplied to the reactor 1 whose internal temperature was controlled to be 850°C under 0.04 MPa. And, these raw material gas components (R31, R22 and TFE) after preheating are supp...
example 2
[0097] The reaction was performed under the same conditions as in Example 1, except that the preset temperature of the electric furnace for heating steam was 800°C, and the internal temperature of the reactor was controlled at 800°C. Next, the gas of the reaction mixture taken out from the outlet of the reactor was treated in the same manner as in Example 1, and the obtained outlet gas was analyzed in the same manner as in Example 1. The results are shown in Table 1 together with the reaction conditions.
example 3
[0099] The reaction was carried out under the same conditions as in Example 1, except that the set temperature of the electric furnace for heating steam was 750°C, and the internal temperature of the reactor was controlled at 750°C. Next, the gas of the reaction mixture taken out from the outlet of the reactor was treated in the same manner as in Example 1, and the obtained outlet gas was analyzed in the same manner as in Example 1. The results are shown in Table 1 together with the reaction conditions.
PUM
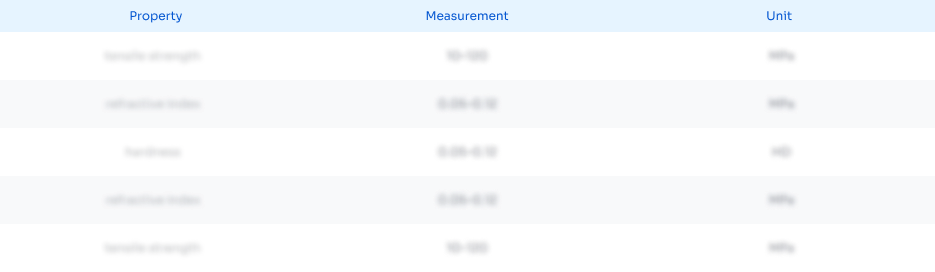
Abstract
Description
Claims
Application Information

- R&D
- Intellectual Property
- Life Sciences
- Materials
- Tech Scout
- Unparalleled Data Quality
- Higher Quality Content
- 60% Fewer Hallucinations
Browse by: Latest US Patents, China's latest patents, Technical Efficacy Thesaurus, Application Domain, Technology Topic, Popular Technical Reports.
© 2025 PatSnap. All rights reserved.Legal|Privacy policy|Modern Slavery Act Transparency Statement|Sitemap|About US| Contact US: help@patsnap.com