Rigidity and flexibility combined pantograph slide plate device
A pantograph sliding plate, rigid-flexible combination technology, used in current collectors, electric vehicles, power collectors, etc., can solve the problem that the number of conductive spots on the contact surface of the pantograph cannot be effectively increased, the effect is not ideal, and the contact resistance is too large problems such as avoiding electrothermal ablation, sharp increase in the number of conductive spots, and reduction in contact pressure
- Summary
- Abstract
- Description
- Claims
- Application Information
AI Technical Summary
Problems solved by technology
Method used
Image
Examples
Embodiment 1
[0022] Step 1: Use 60K polyacrylonitrile-based carbon fiber and its high-temperature (2500-3300°C) graphitized graphite fiber and copper fiber to carry out three-dimensional three-dimensional weaving according to a certain ratio, and the proportion of copper is not less than 15%. (mass percentage), woven into a prefabricated body whose shape meets the requirements;
[0023] Step 2, brushing the bottom surface of the prefabricated body so that the surface is covered with a layer of fibers; the fiber length is 2-5 mm, and spraying a layer of copper powder on the fibers on the bottom surface of the prefabricated body;
[0024] Step 3, the substrate is derusted, decontaminated, and frosted, and then coated with a uniform thickness of conductive adhesive;
[0025] Step 4, spread the prefabricated body on the substrate, compact it, and heat-cure according to a special curing procedure;
[0026] Step 5, install the copper-impregnated carbon slide 1 and the above-mentioned flexible s...
Embodiment 2
[0028] Step 1, using polyacrylonitrile fiber as raw material, processing it into a felt according to the required thickness of 30 mm, after pre-oxidation and carbonization, and then graphitizing at a high temperature at 2500-3000 ° C to make graphite felt;
[0029] Step 2, cutting the graphite felt into the required size; wherein the width of the felt is 50mm;
[0030] Step 3, using molten metal high-pressure carbon impregnation technology to impregnate graphite felt with nickel to obtain nickel-impregnated graphite felt;
[0031] Step 4, spray a layer of copper powder on the bottom of the graphite felt;
[0032] Step 5, the substrate is derusted, decontaminated, and frosted, and then coated with conductive adhesive of uniform thickness;
[0033] Step 6, spread the prefabricated body on the base plate, compact it, and heat-cure according to a special curing procedure;
[0034] Step 7, install the copper-impregnated carbon slide 1 and the above-mentioned flexible slide 2 on t...
Embodiment 3
[0036] Step 1, use 48K polyacrylonitrile-based carbon fiber and its high-temperature (2500-3300°C) graphitized graphite fiber and copper fiber. The proportion of the three according to the copper (mass percentage) is not less than 35%, and the carbon fiber is not less than 25%. %, use the needle punching felting process to make graphite felt with a composite design of thickness, and then cut it into the required size, wherein the width is 40mm;
[0037] Steps 2-5 correspond to steps 4-7 in Embodiment 2.
PUM
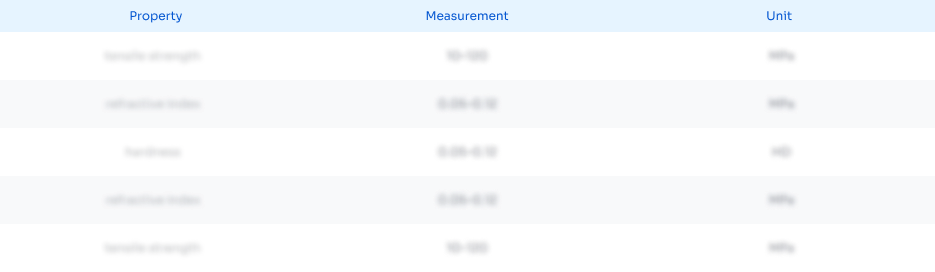
Abstract
Description
Claims
Application Information

- Generate Ideas
- Intellectual Property
- Life Sciences
- Materials
- Tech Scout
- Unparalleled Data Quality
- Higher Quality Content
- 60% Fewer Hallucinations
Browse by: Latest US Patents, China's latest patents, Technical Efficacy Thesaurus, Application Domain, Technology Topic, Popular Technical Reports.
© 2025 PatSnap. All rights reserved.Legal|Privacy policy|Modern Slavery Act Transparency Statement|Sitemap|About US| Contact US: help@patsnap.com