Charcoal preparation method and special charcoal preparation drying device during carbon disulfide production
A carbon disulfide and drying device technology, applied in drying, drying machine, heating device and other directions, can solve the problems of reducing production efficiency, hindering the normal progress of the reaction, incomplete moisture drying, etc., and achieving the effect of reducing the consumption of raw materials
- Summary
- Abstract
- Description
- Claims
- Application Information
AI Technical Summary
Problems solved by technology
Method used
Image
Examples
Embodiment 1
[0025] Embodiment 1: refer to figure 1 , is a schematic structural view of the carbon preparation drying device used in Example 1 of the present invention, including a drying chamber 18 composed of a housing 13, the drying chamber 18 is provided with a feed inlet 16, a dry air outlet 17, and a dry air inlet A14 , discharge port 11 and discharge door 12, a heating interlayer 10 is provided on the periphery of the housing 13 that constitutes the drying chamber 18, and the heating interlayer 10 is provided with a heat medium inlet 19 and a heat medium outlet 15, the central position of the drying chamber A central drying air intake mechanism is provided, and the central drying air intake mechanism includes a vertical distributor 31 and a dry air inlet B (33). The distributor 31 is a vertical pipe body, and the pipe body wall is provided with Uniformly distributed gas outlet 32, the gas outlet 32 is from the inside of the distributor 31 pipe body to the outside of the pipe body ...
Embodiment 2
[0029] Embodiment 2: refer to figure 2 , is a schematic structural diagram of the carbon preparation drying device used in Embodiment 2 of the present invention. Compared with Embodiment 1, the difference of this embodiment is that the distributor 31 of the drying air intake mechanism in the drying chamber consists of multiple parallel Vertical pipe body composition.
Embodiment 3
[0030] Embodiment 3: refer to image 3 , is a schematic structural diagram of the carbon preparation drying device used in Example 3 of the present invention. Compared with the previous embodiments, the difference of this embodiment is that the dry air inlet A14 extends into the drying chamber 18 and the front end The air outlet is curved downward. Certainly, the air outlet 32 of the distributor 31 may also have the same or similar structure.
PUM
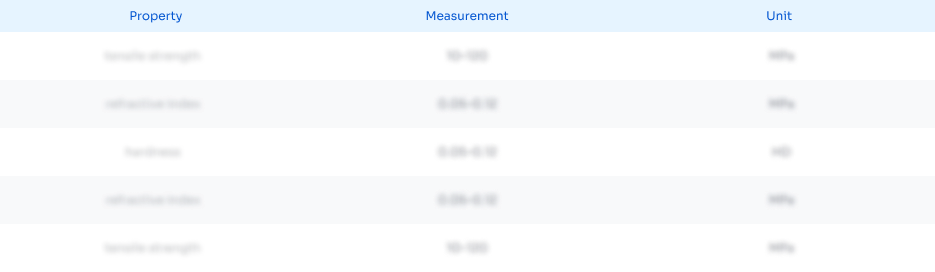
Abstract
Description
Claims
Application Information

- R&D
- Intellectual Property
- Life Sciences
- Materials
- Tech Scout
- Unparalleled Data Quality
- Higher Quality Content
- 60% Fewer Hallucinations
Browse by: Latest US Patents, China's latest patents, Technical Efficacy Thesaurus, Application Domain, Technology Topic, Popular Technical Reports.
© 2025 PatSnap. All rights reserved.Legal|Privacy policy|Modern Slavery Act Transparency Statement|Sitemap|About US| Contact US: help@patsnap.com