Preparation method of boron-containing steel preventing casting blank corner cracking
A boron steel and corner cracking technology is applied in the field of preparing boron-containing steel for preventing corner cracking of casting billets, and can solve the problems such as easy cracks in the corners of boron-containing steel billets.
- Summary
- Abstract
- Description
- Claims
- Application Information
AI Technical Summary
Problems solved by technology
Method used
Image
Examples
Embodiment
[0028] Example: SS400 steel
[0029] 1 According to the mass percentage of the chemical composition of boron steel, it contains: C0.17, Si0.12, Mn0.36, P0.009, S0.014, N0.0041, B0.0008; the balance is Fe.
[0030] 2 The process route is:
[0031] Hot metal pretreatment-converter smelting-external refining-ti addition-continuous casting-reheating-hot continuous rolling-inspection and storage.
[0032] 3 The main process measures of the preparation method
[0033] Steelmaking process: Traditional converter steelmaking is used for production. After tapping, argon gas is blown behind the furnace for 5 minutes, and the flow rate of argon gas is 0.4m 3 / min, argon blowing pressure 0.5MPa; starting from 1 / 4 of the tapping weight, start to add 350kg / 180 tons of aluminum and iron to the ladle for pre-deoxidation, add ferromanganese and ferrosilicon according to the content of Mn and Si in the final boron steel for alloying, and at the same time Add 500-600kg / 180 tons of active lime ...
PUM
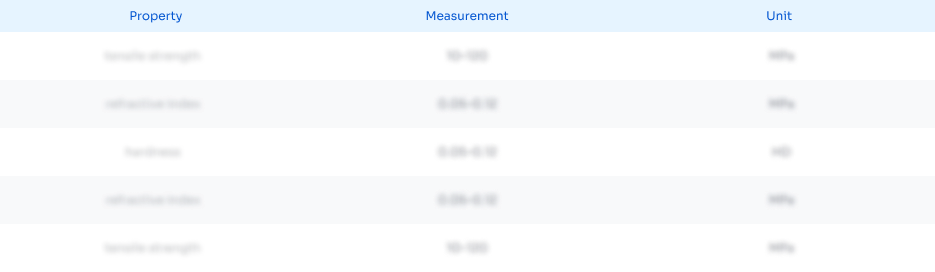
Abstract
Description
Claims
Application Information

- R&D Engineer
- R&D Manager
- IP Professional
- Industry Leading Data Capabilities
- Powerful AI technology
- Patent DNA Extraction
Browse by: Latest US Patents, China's latest patents, Technical Efficacy Thesaurus, Application Domain, Technology Topic, Popular Technical Reports.
© 2024 PatSnap. All rights reserved.Legal|Privacy policy|Modern Slavery Act Transparency Statement|Sitemap|About US| Contact US: help@patsnap.com