Method for preparing dispersing agent for coating by naphthalenesulfonate wastewater
A naphthalene sulfonate and dispersant technology, applied in powder coatings, coatings, etc., can solve the problems of lipophilic groups without carbon chain length and poor bonding, and achieve simple preparation methods, good solubility and bonding sexual effect
- Summary
- Abstract
- Description
- Claims
- Application Information
AI Technical Summary
Problems solved by technology
Method used
Examples
example 1
[0017] First get 900mL naphthalenesulfonate waste water and put it into a centrifuge, carry out centrifugation, get the supernatant, put the supernatant of gained in the container, use the sodium hydroxide solution that the mass fraction is 68% to adjust the pH to 7.5, then add 600mL of ethylene glycol to it, stir evenly, and stand still for 10min; then put the mixed solution in the above container into an Erlenmeyer flask with a thermometer, a stirrer and a spherical condenser, and then add 10g of zeolite therein, Set the rotation speed at 160r / min, the temperature at 110°C, and after refluxing for 40min, cool down to 60°C, then drop 300mL of methylene succinic acid into the container with a burette at a rate of 10d / min; After the addition is completed, cool down to 40°C, stop stirring, and after standing still for 35 minutes, filter under reduced pressure while hot, collect the filtrate, put the obtained filtrate into the reaction kettle, add 120g of potassium persulfate to i...
example 2
[0020]First get 1050mL naphthalene sulfonate waste water and put into centrifuge, carry out centrifugation, get supernatant, the supernatant of gained is put into container, use the sodium hydroxide solution that massfraction is 68% to adjust pH to 7.8, then add 700mL ethylene glycol to it, stir evenly, and stand still for 13min; then put the mixed solution in the above container into an Erlenmeyer flask with a thermometer, a stirrer and a spherical condenser, and then add 13g zeolite therein, Set the rotation speed at 170r / min, the temperature at 130°C, and after refluxing for 55 minutes, cool down to 65°C, then use a burette to drop 350mL of methylene succinic acid into the container at a rate of 15d / min; After the addition is completed, lower the temperature to 45°C, stop stirring, and after standing still for 40 minutes, filter under reduced pressure while hot, collect the filtrate, put the obtained filtrate into the reaction kettle, add 135g of potassium persulfate to it, ...
example 3
[0023] First get 1200mL naphthalene sulfonate waste water and put into centrifuge, carry out centrifugation, get supernatant, the supernatant of gained is put into container, use the sodium hydroxide solution that massfraction is 68% to adjust pH to 8.0, then add 800mL ethylene glycol therein, stir evenly, stand still for 15min; then put the mixed solution in the above-mentioned container in the Erlenmeyer flask with thermometer, stirrer and spherical condenser, add 15g zeolite therein again, Set the rotation speed at 180r / min, the temperature at 150°C, and after reflux for 70min, cool down to 70°C, then use a burette to drop 400mL of methylene succinic acid into the container at a rate of 20d / min; After the addition is completed, lower the temperature to 50°C, stop stirring, and after standing still for 45 minutes, filter under reduced pressure while hot, collect the filtrate, put the obtained filtrate into the reaction kettle, add 150g of potassium persulfate to it, stir even...
PUM
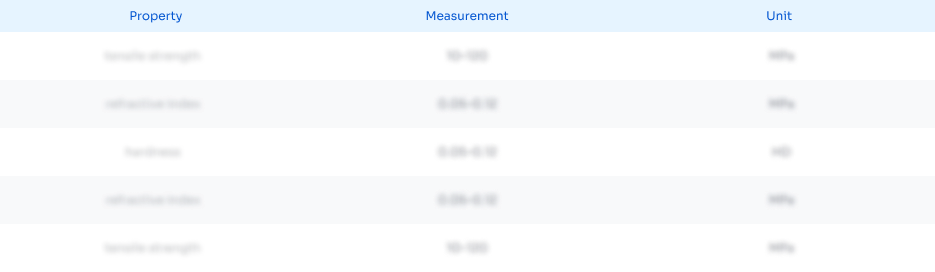
Abstract
Description
Claims
Application Information

- R&D Engineer
- R&D Manager
- IP Professional
- Industry Leading Data Capabilities
- Powerful AI technology
- Patent DNA Extraction
Browse by: Latest US Patents, China's latest patents, Technical Efficacy Thesaurus, Application Domain, Technology Topic, Popular Technical Reports.
© 2024 PatSnap. All rights reserved.Legal|Privacy policy|Modern Slavery Act Transparency Statement|Sitemap|About US| Contact US: help@patsnap.com