Fluorine-silicon modified acrylate emulsion and preparation method thereof
An acrylate and modified technology, used in dyeing, textile and papermaking, fiber processing, etc., can solve the problems of low surface energy, low glass transition temperature, too soft film of silicone series compounds, etc. Low, prevent dye migration, reduce the effect of VOC emission
- Summary
- Abstract
- Description
- Claims
- Application Information
AI Technical Summary
Problems solved by technology
Method used
Examples
Embodiment 1
[0027] Example 1 is composed of the following materials in parts by weight: Acrylic acid 5.0, ethyl acrylate 8.0, glycidyl acrylate 0.5, octamethylcyclotetrasiloxane (D4) 3.0, trifluoroethyl acrylate 8.0, alkylethylene Sodium sulfonate 5.0, potassium persulfate 0.5, deionized water 70.0
[0028] First, potassium persulfate is added into the catalyst tank equipped with deionized water, and stirred evenly to obtain a concentration of 2.5% initiator solution A; acrylic acid, ethyl acrylate, glycidyl acrylate, octamethylcyclotetrasiloxane ( D4) Mix trifluoroethyl acrylate in the premixing tank evenly to obtain the mixed phase B of polymerized monomers; add sodium alkyl vinyl sulfonate and deionized water into the four-necked flask, maintain the rotation speed at 200r / min, and heat After reaching 85°C, slowly add the uniformly mixed monomer mixed phase B and 90% initiator solution A for 1 hour, and keep the polymerization temperature at 85°C during the reaction process; At the sam...
Embodiment 2
[0029] Example 2 is composed of the following materials in parts by weight: methyl acrylate 12.0, octyl acrylate 10.0, glycidyl methacrylate 1.0, hexamethylcyclotrisiloxane (D3) 3.0, hexafluorobutyl methacrylate Ester 6.0, Sodium Lauryl Allyl Succinate 2.0, Ammonium Persulfate 1.0, Deionized Water 65.0
[0030] First, ammonium persulfate is added to the catalyst tank equipped with deionized water, and stirred evenly to obtain an initiator solution A with a concentration of 2.5%; methyl acrylate, octyl acrylate, glycidyl methacrylate, hexamethylcyclotri Mix siloxane (D3) and hexafluorobutyl methacrylate evenly in the premixing tank to obtain the mixed phase B of polymerized monomers; add sodium dodecyl allyl succinate and deionized water into a four-necked flask , the rotating speed is maintained at 250r / min, after heating to 70°C, slowly add the homogeneously mixed monomer mixed phase B and 90% initiator solution A for 3 hours, and the reaction process maintains the polymeriza...
Embodiment 3
[0031] Example 3 is composed of the following materials in parts by weight: methacrylic acid 9.0, butyl acrylate 12.0, glycidyl methacrylate 0.5, decamethylcyclopentasiloxane (D5) 8.0, trifluoroethyl methacrylate Ester 3.0, sodium vinyl sulfonate 8.0, ammonium persulfate 0.5, deionized water 60.0
[0032] First, ammonium persulfate is added to the catalyst tank equipped with deionized water, and stirred evenly to obtain a concentration of 2.5% initiator solution A; methacrylic acid, butyl acrylate, glycidyl methacrylate, decamethylcyclopentadiene Mix siloxane (D5) and trifluoroethyl methacrylate evenly in the premixing tank to obtain the mixed phase B of polymerized monomers; add sodium vinyl sulfonate and deionized water into a four-necked flask, and maintain the rotation speed at 300r / min, after heating to 90°C, slowly drop the homogeneously mixed monomer mixed phase B and 90% initiator solution A for 1 hour, and keep the polymerization temperature at 90°C during the reacti...
PUM
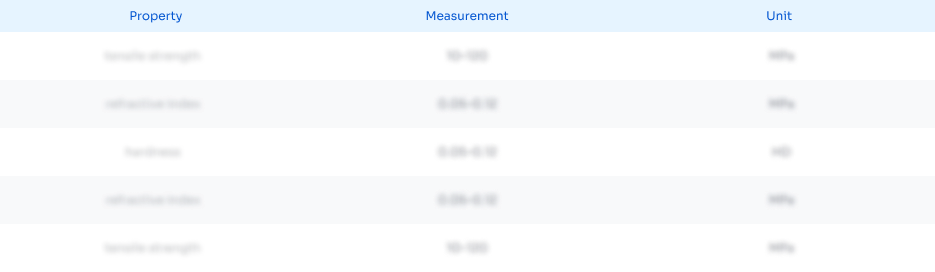
Abstract
Description
Claims
Application Information

- R&D Engineer
- R&D Manager
- IP Professional
- Industry Leading Data Capabilities
- Powerful AI technology
- Patent DNA Extraction
Browse by: Latest US Patents, China's latest patents, Technical Efficacy Thesaurus, Application Domain, Technology Topic, Popular Technical Reports.
© 2024 PatSnap. All rights reserved.Legal|Privacy policy|Modern Slavery Act Transparency Statement|Sitemap|About US| Contact US: help@patsnap.com