A method for composite casting of large alloy steel ingots with mold core integration
A technology of composite steel and alloy steel, which is applied in the field of composite casting of metal materials, can solve the problems of difficult fixing of bars and cumbersome cloth distribution, and achieve the effect of increasing solidification speed, increasing solidification speed and reducing production cost
- Summary
- Abstract
- Description
- Claims
- Application Information
AI Technical Summary
Problems solved by technology
Method used
Image
Examples
Embodiment 1
[0032] A method for integrated composite casting of a large alloy steel ingot with a mold core, taking a large 20CrMoV low alloy steel ingot with a weight of 160 tons as an example by vacuum pouring in the above-injection steel casting method, the steps of the method are as follows:
[0033] a. If Figure 1-Figure 4 and Figure 6 As shown, the selected quality qualified material is 20CrMoV, six rolling slabs with a size of 120mm * 1600mm * 3120mm, and a piece of rolling slabs with a size of 120mm * 1600mm * 3440mm, as the slab for welding steel ingot mold 4, The surface of the slab is cleaned, degreased and dried according to figure 1 and figure 2 As shown, a rolling slab with a size of 120mm * 1600mm * 3440mm is used as the mold bottom of the ingot mold 4, and two rolling slabs with a size of 120mm * 1600mm * 3120mm are used to make the sides of the ingot mold 4, and four A rolled slab with a size of 120mm×1600mm×3120mm is used as the front and back of the ingot mold 4, a...
Embodiment 2
[0039] A method for integrated composite casting of a large alloy steel ingot with a mold core. The method of casting and preparing a 45-ton 304 stainless steel / 16Mn low-alloy steel large composite steel ingot under the protection of argon by using the above injection method is an example. The steps of the method are as follows:
[0040] a. If Figure 1-Figure 4 and Figure 6 As shown, the quality qualified material is selected as 304 stainless steel, six rolled slabs with a size of 80mm * 1000mm * 2400mm and a piece of rolled slabs with a size of 80mm * 1000mm * 2000mm are used as slabs for welding steel ingot mold 4, Clean, degrease and dry the surface of the slab according to figure 1 and figure 2 As shown, a rolling slab with a size of 80mm * 1000mm * 2000mm is used as the mold bottom of the ingot mold 4, and two rolling slabs with a size of 80mm * 1000mm * 2400mm are used to make the side of the ingot mold 4, and four A rolled slab with a size of 80mm×1000mm×2400mm is...
Embodiment 3
[0046] A method for integrated composite casting of a large alloy steel ingot with a mold core, taking a downcast steel casting method and pouring and preparing a 90-ton large Q345B steel ingot under a protective atmosphere as an example, the steps of the method are as follows:
[0047] a. If Figure 1-Figure 3 and Figure 5-Figure 6 As shown, select two rolled slabs with qualified quality Q345B, with a size of 100mm×1500mm×3200mm, two rolled slabs with a size of 100mm×2000mm×3200mm and a rolled slab with a size of 150mm×2000mm×1700mm A piece of slab is used as a slab for welding steel ingot mold 4, and the surface of the slab is cleaned, degreased, and dried according to figure 1 and figure 2 As shown, a rolling slab with a size of 150mm * 2000mm * 1700mm is used as the bottom of the ingot mold 4, and two rolling slabs with a size of 100mm * 1500mm * 3200mm are used to make the sides of the ingot mold 4. A rolled slab with a size of 100mm×2000mm×3200mm is used as the fron...
PUM
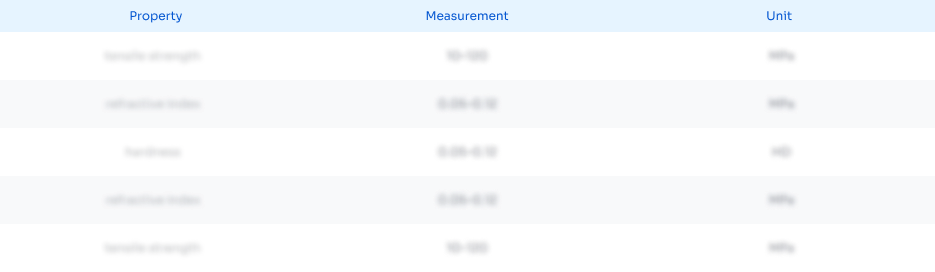
Abstract
Description
Claims
Application Information

- R&D
- Intellectual Property
- Life Sciences
- Materials
- Tech Scout
- Unparalleled Data Quality
- Higher Quality Content
- 60% Fewer Hallucinations
Browse by: Latest US Patents, China's latest patents, Technical Efficacy Thesaurus, Application Domain, Technology Topic, Popular Technical Reports.
© 2025 PatSnap. All rights reserved.Legal|Privacy policy|Modern Slavery Act Transparency Statement|Sitemap|About US| Contact US: help@patsnap.com