Method for repairing high-temperature alloy thin-walled cartridge receiver part through precision pulse welding
A technology of pulse welding and high temperature alloys, applied in welding equipment, welding equipment, auxiliary welding equipment, etc., can solve the problems of non-concentration of welding arc and deformation of parts, and achieve control of welding deformation, interlayer temperature, and reduction of welding stress level. Effect
- Summary
- Abstract
- Description
- Claims
- Application Information
AI Technical Summary
Problems solved by technology
Method used
Image
Examples
Embodiment Construction
[0035] The present invention will be further elaborated below in conjunction with the accompanying drawings of the description.
[0036] The method for repairing superalloy thin-wall casing parts by precision pulse welding in the present invention mainly includes: 1) predicting the welding deformation trend and analyzing the internal stress state of the parts after use; 2) reducing heat input and optimizing the welding process route; 3) Design special welding tooling to control parts deformation and welding pollution oxidation. Specifically include the following steps:
[0037] According to the defect length and position of thin-walled casing parts, combined with numerical simulation technology, the failure mode and stress state of parts are analyzed;
[0038] Accurately measure the front and rear mounting edges of the casing and other relevant dimensions before welding;
[0039] Use X-ray inspection and color inspection to determine defect location and size;
[0040] Proce...
PUM
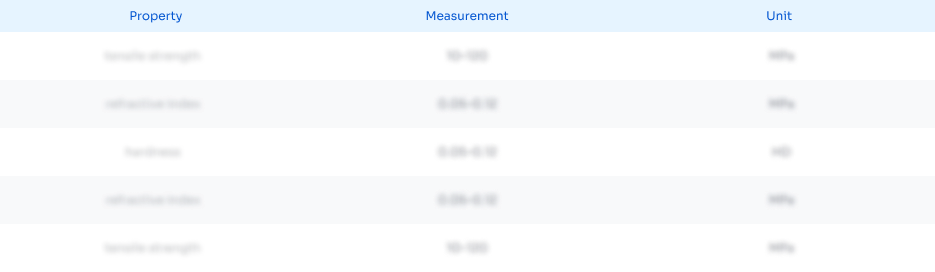
Abstract
Description
Claims
Application Information

- R&D Engineer
- R&D Manager
- IP Professional
- Industry Leading Data Capabilities
- Powerful AI technology
- Patent DNA Extraction
Browse by: Latest US Patents, China's latest patents, Technical Efficacy Thesaurus, Application Domain, Technology Topic, Popular Technical Reports.
© 2024 PatSnap. All rights reserved.Legal|Privacy policy|Modern Slavery Act Transparency Statement|Sitemap|About US| Contact US: help@patsnap.com