Wear resistant and high-hardness diamond glaze, preparation method and application
A high-hardness, diamond technology, applied in the field of ceramic glaze, can solve the problems of low hardness and poor wear resistance, and achieve the effect of improving wear resistance and hardness
- Summary
- Abstract
- Description
- Claims
- Application Information
AI Technical Summary
Problems solved by technology
Method used
Image
Examples
Embodiment 1
[0061] In terms of mass percentage, 10% kaolin, 8.4% andalusite, 7.5% potassium feldspar, 6.7% leucite, 2.2% grossular garnet, 13.5% nepheline from Norway, 12.2% spodumene, wollastonite 4.5%, 7.5% quartz, 7% zircon sand, 12.5% white corundum, 3% dolomite, 2.2% calcined white talc, 0.4% zinc oxide, and 2.2% additives. Material formula. Among them, in terms of mass percentage, the particle gradation of andalusite is 50μm accounting for 20%; The particle gradation of white corundum is 50 μm accounting for 15%; the particle grading of quartz is <5 μm accounting for 25%, 5-20 μm accounted for 35%, 20-50 μm accounted for 40%; the particle size distribution of zircon sand was <5 μm, accounting for 45%, and 5-20 μm accounted for 55%. Among them, the additives are 10% sodium tripolyphosphate, 40% aluminum tripolyphosphate, and 50% polyanionic cellulose in terms of mass percentage. According to the glaze formula, the ingredients are fed into the ball mill, and the glaze slurry that...
Embodiment 2
[0067] In terms of mass percentage, 8% kaolin, 8% andalusite, 9.7% potassium feldspar, 8.8% leucite, 2% grossular garnet, 10% nepheline from Norway, 10% spodumene, wollastonite 5.8%, 9.7% quartz, 9.1% zircon sand, 10.5% white corundum, 2.8% dolomite, 2% calcined white talc, 0.4% zinc oxide, and 2.2% additives. Material formula. Among them, in terms of mass percentage, the particle gradation of andalusite is 50μm accounting for 20%; The particle gradation of white corundum is 50 μm accounting for 15%; the particle grading of quartz is <5 μm accounting for 25%, 5-20 μm accounted for 35%, 20-50 μm accounted for 40%; the particle size distribution of zircon sand was <5 μm, accounting for 45%, and 5-20 μm accounted for 55%. Among them, the additives are 10% sodium tripolyphosphate, 40% aluminum tripolyphosphate, and 50% polyanionic cellulose in terms of mass percentage. According to the glaze formula, the ingredients are fed into the ball mill, and the glaze slurry that has reac...
PUM
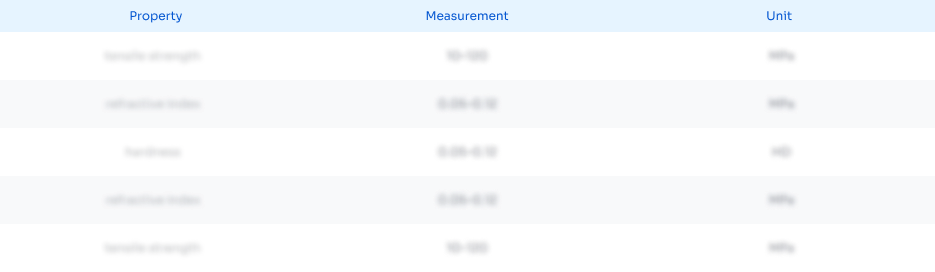
Abstract
Description
Claims
Application Information

- R&D
- Intellectual Property
- Life Sciences
- Materials
- Tech Scout
- Unparalleled Data Quality
- Higher Quality Content
- 60% Fewer Hallucinations
Browse by: Latest US Patents, China's latest patents, Technical Efficacy Thesaurus, Application Domain, Technology Topic, Popular Technical Reports.
© 2025 PatSnap. All rights reserved.Legal|Privacy policy|Modern Slavery Act Transparency Statement|Sitemap|About US| Contact US: help@patsnap.com