Preparation method of rock wool/corn straw fiber composite heat insulation material
A technology of corn straw fiber and composite thermal insulation materials, which is applied in the direction of sustainable waste treatment, solid waste management, climate sustainability, etc., can solve problems such as poor interface compatibility, affecting product production speed, mechanical strength, and slow resin penetration speed , to reduce specific gravity, improve wetting speed and interfacial compatibility, increase production speed and mechanical strength
- Summary
- Abstract
- Description
- Claims
- Application Information
AI Technical Summary
Problems solved by technology
Method used
Examples
Embodiment 1
[0017] Press 400kg of rock wool and 100kg of corn stalk fibers into thin sheets respectively, and arrange the rock wool and corn stalk fiber sheets at intervals on a pendulum machine (that is, one layer of rock wool, one layer of corn stalk fiber, one layer of rock wool, etc.) to form a superimposed cotton layer of a certain thickness, and the superimposed cotton layer enters the discount machine to squeeze and discount. Immerse the cotton layer in phenolic resin, cure at high temperature, and cut it to the required size. Compared with pure rock wool products, the specific gravity of the product with this formula is reduced by 25%, the dipping speed is increased by 18-29%, and the mechanical strength is increased by 18-28%.
Embodiment 2
[0019] Press 350kg of rock wool and 150kg of corn stalk fiber into thin sheets respectively, and arrange the rock wool and corn stalk fiber sheets at intervals on the pendulum machine to form a certain thickness of superimposed cotton layer, and the superimposed cotton layer enters the folding machine for extrusion Discount. Immerse the cotton layer in phenolic resin, cure at high temperature, and cut it to the required size. Compared with pure rock wool products, the specific gravity of the product with this formula is reduced by 36%, the dipping speed is increased by 22-35%, and the mechanical strength is increased by 15-25%.
Embodiment 3
[0021] Press 425kg of rock wool and 75kg of corn stalk fibers into thin sheets respectively, and arrange the prepared rock wool and corn stalk fiber sheets at intervals on the pendulum machine to form a certain thickness of superimposed cotton layer, and the superimposed cotton layer enters the folding machine for extrusion Discount. Immerse the cotton layer in phenolic resin, cure at high temperature, and cut it to the required size. Compared with pure rock wool products, the specific gravity of the product with this formula is reduced by 22%, the dipping speed is increased by 16-22%, and the mechanical strength is increased by 15-24%.
PUM
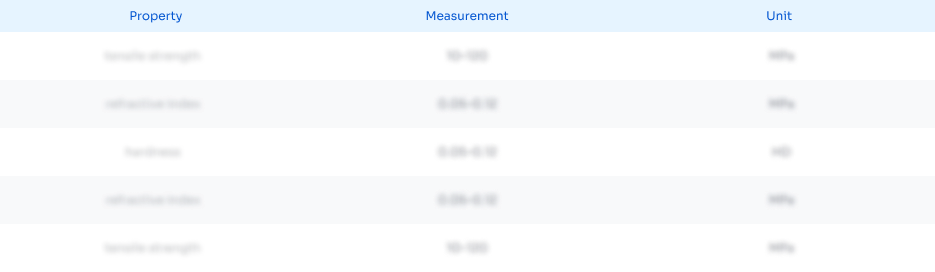
Abstract
Description
Claims
Application Information

- R&D
- Intellectual Property
- Life Sciences
- Materials
- Tech Scout
- Unparalleled Data Quality
- Higher Quality Content
- 60% Fewer Hallucinations
Browse by: Latest US Patents, China's latest patents, Technical Efficacy Thesaurus, Application Domain, Technology Topic, Popular Technical Reports.
© 2025 PatSnap. All rights reserved.Legal|Privacy policy|Modern Slavery Act Transparency Statement|Sitemap|About US| Contact US: help@patsnap.com