Ramming mass for air-supplying blowpipe of blast furnace and forming method thereof
A molding method and technology of ramming materials, which are applied in the field of ramming materials for blast furnaces, can solve the problems of easy burn-through and damage, unsatisfactory thermal insulation of blast furnace air blowing pipes, etc., and achieve good thermal insulation performance, excellent thermal stability, and convenient production Effect
- Summary
- Abstract
- Description
- Claims
- Application Information
AI Technical Summary
Problems solved by technology
Method used
Examples
Embodiment 1
[0026] Raw material ratio: 70 parts of water slag, 22 parts of high-temperature cement, 8 parts of refractory clinker powder, and 8 parts of water.
[0027] Molding method: place the blowpipe to be made at an angle of 45°, close the lower end, and put it into the mold. The mold requires a taper of 0.7° to facilitate demoulding, and wrap a layer of linoleum on the surface of the mold to facilitate demoulding. Next, water slag, high-temperature cement, and refractory clinker powder weighed according to the formula ratio were added into water, mixed and stirred for 4 minutes until uniform. Feed the evenly mixed material into the blowpipe, pound the material until it is dense with a wooden stick while feeding, until the whole blowpipe is formed, and then take out the mold to repeat the next one. The molded blowpipe can be placed at room temperature and can be used within 7 days without baking.
Embodiment 2
[0029] Raw material ratio: 65 parts of water slag, 24 parts of high-temperature cement, 10 parts of refractory clinker powder, and 12 parts of water.
[0030] Molding method: place the blowpipe to be produced at an angle of 40°, close the lower end, and put it into the mold. The mold requires a taper of 1° to facilitate demoulding, and wrap a layer of felt on the surface of the mold to facilitate demoulding. Next, water slag, high-temperature cement, and refractory clinker powder weighed according to the formula ratio were added into water and mixed and stirred for 5 minutes until uniform. Feed the evenly mixed material into the blowpipe, pound the material until it is dense with a wooden stick while feeding, until the whole blowpipe is formed, and then take out the mold to repeat the next one. The molded blowpipe is placed at room temperature and can be used after 9 days without baking.
Embodiment 3
[0032] Raw material ratio: 75 parts of water slag, 20 parts of high-temperature cement, 6 parts of refractory clinker powder, and 5 parts of water.
[0033] Molding method: place the blowpipe to be made at an angle of 50°, close the lower end, and put it into the mold. The mold requires a taper of 0.5° to facilitate demoulding, and wrap a thin iron sheet on the surface of the mold to facilitate demoulding. Next, water slag, high-temperature cement, and refractory clinker powder weighed according to the formula ratio were added into water and mixed and stirred for 3 minutes until uniform. Feed the evenly mixed material into the blowpipe, pound the material until it is dense with a wooden stick while feeding, until the whole blowpipe is formed, and then take out the mold to repeat the next one. The molded blowpipe is placed at room temperature and can be used within 5 days without baking.
PUM
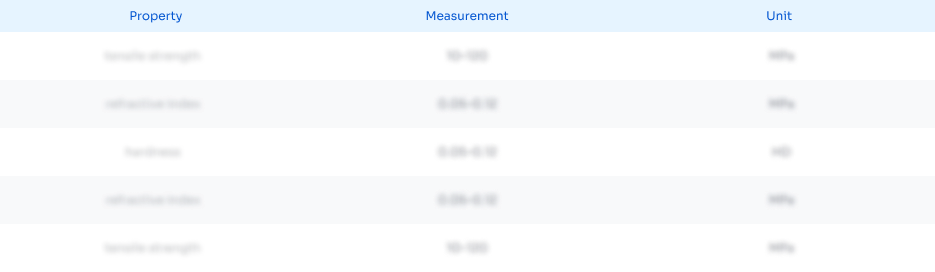
Abstract
Description
Claims
Application Information

- R&D Engineer
- R&D Manager
- IP Professional
- Industry Leading Data Capabilities
- Powerful AI technology
- Patent DNA Extraction
Browse by: Latest US Patents, China's latest patents, Technical Efficacy Thesaurus, Application Domain, Technology Topic, Popular Technical Reports.
© 2024 PatSnap. All rights reserved.Legal|Privacy policy|Modern Slavery Act Transparency Statement|Sitemap|About US| Contact US: help@patsnap.com