Incineration boiler for high-concentration salty organic waste liquid
A high-concentration salt-containing and organic waste liquid technology is applied in the field of high-concentration salt-containing organic waste liquid incineration boilers and high-concentration chemical salt-containing organic waste liquid incineration boilers. Clogging and other problems, to achieve the effect of simple manufacturing process, reduced processing costs, and convenient maintenance
- Summary
- Abstract
- Description
- Claims
- Application Information
AI Technical Summary
Problems solved by technology
Method used
Image
Examples
Embodiment
[0022] Such as figure 1 A kind of high-concentration chemical salt-containing organic waste liquid incineration boiler shown, the arrow direction indicates the direction of high temperature flue gas from waste liquid incineration; its structure mainly includes: its structure mainly includes: adiabatic combustion chamber (1), adiabatic combustion turning chamber ( 22), adiabatic combustion turning chamber smoke shielding wall (23), quenching chamber (24), quenching film wall tube panel (25), convection cooling chamber I (10), convection evaporation tube panel I (11), convection cooling chamber II (12), convection evaporation tube panel II (13), convection cooling chamber III (14), convection evaporation tube panel III (15), expansion joint (16), high temperature section economizer (17), medium temperature section coal saving (18), low-temperature section economizer (19), boiler flue gas outlet (20), molten salt cooling tank (27), molten salt reheating burner (34), feed water pre...
PUM
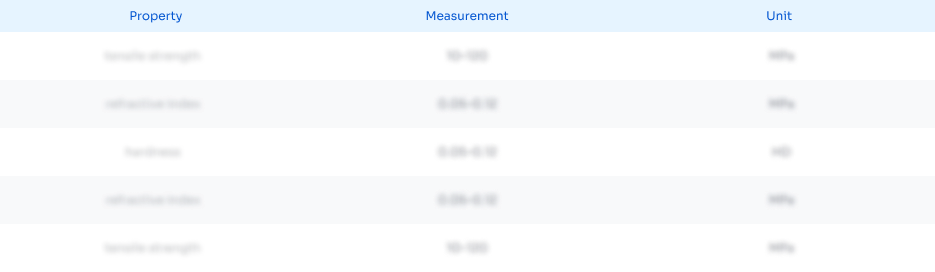
Abstract
Description
Claims
Application Information

- R&D
- Intellectual Property
- Life Sciences
- Materials
- Tech Scout
- Unparalleled Data Quality
- Higher Quality Content
- 60% Fewer Hallucinations
Browse by: Latest US Patents, China's latest patents, Technical Efficacy Thesaurus, Application Domain, Technology Topic, Popular Technical Reports.
© 2025 PatSnap. All rights reserved.Legal|Privacy policy|Modern Slavery Act Transparency Statement|Sitemap|About US| Contact US: help@patsnap.com