Cotton fabric hydrophobic finishing method based on acetic anhydride-acrylics-electron beam technique
A technology of acrylates and acetic anhydride pre-esters, applied in fiber processing, plant fibers, textiles and papermaking, etc., can solve the problems that low surface substances cannot effectively cover fabrics, and the hydrophobicity of fabrics cannot be improved, so as to avoid pollution and cost. Problem, significant social and economic significance, small effect of fabric damage
- Summary
- Abstract
- Description
- Claims
- Application Information
AI Technical Summary
Problems solved by technology
Method used
Image
Examples
Embodiment 1
[0029] Fabric: pure cotton woven fabric (40S×40S / 133*72)
[0030] 1) Cotton fiber pre-esterified with acetic anhydride
[0031] Prescription: Acetic Anhydride
[0032] Iodine 2g / L
[0033] Bath ratio 1:25
[0034] Method: The cotton fabric is soaked in the above-mentioned acetic anhydride, and treated at room temperature for 2 hours. Reduction with saturated sodium thiosulfate until the dye solution is colorless, washed with water and dried for later use.
[0035] 2) After the cotton fabric is soaked in the organic solution containing acrylate compounds for 1 min, the excess solution is pressed by the paddle
[0036] Prescription: n-Hexyl Methacrylate: 20%
[0038] Method: The fabric is dipped and rolled in the reaction solution once, and the excess rate is about 60%.
[0039] 3) After electron beam irradiation, oven dry the fabric
[0040] Method: The irradiation dose is 33KGy, and the oven is dried at 105°C for 2 minutes after irradiation. ...
Embodiment 2
[0046] Fabric: pure cotton woven fabric (40S×40S / 133*72)
[0047] 1) Cotton fiber pre-esterified with acetic anhydride
[0048] Prescription: Acetic Anhydride
[0049] Iodine 1g / L
[0050] Bath ratio 1:25
[0051] Method: The cotton fabric is soaked in the above-mentioned acetic anhydride, and treated at room temperature for 3 hours. Reduction with saturated sodium thiosulfate until the dye solution is colorless, washed with water and dried for later use.
[0052] 2) After the cotton fabric is soaked in an organic solution containing acrylate compounds for 10 minutes, the excess solution is pressed by a paddle
[0053] Prescription: Stearyl Acrylate: 50%
[0055] Method: The fabric is soaked and rolled in the reaction solution once, and the rolling rate is about 100%.
[0056] 3) After electron beam irradiation, oven dry the fabric
[0057]Method: The irradiation dose is 45KGy, and the oven is dried at 60°C after irradiation.
[0058] Table 2...
Embodiment 3
[0063] Fabric: pure cotton woven fabric (40S×40S / 133*72)
[0064] 1) Cotton fiber pre-esterified with acetic anhydride
[0065] Prescription: Acetic Anhydride
[0066] Iodine 3g / L
[0067] Bath ratio 1:40
[0068] Method: The cotton fabric is soaked in the above-mentioned acetic anhydride, and treated at room temperature for 1 hour. Reduction with saturated sodium thiosulfate until the dye solution is colorless, washed with water and dried for later use.
[0069] 2) After the cotton fabric is soaked in an organic solution containing acrylate compounds, the excess solution is pressed by a paddle
[0070] Prescription: lauryl acrylate and n-octadecyl methacrylate (1:1g / g): 20%
[0071] Solvent: methanol + isopropanol + butanol (1:1:1)
[0072] Method: The fabric is dipped in the reaction solution once and rolled, and the rolling rate is about 100%.
[0073] 3) After electron beam irradiation, oven dry the fabric
[0074] Method: The irradiation dose is 65KGy, and the ove...
PUM
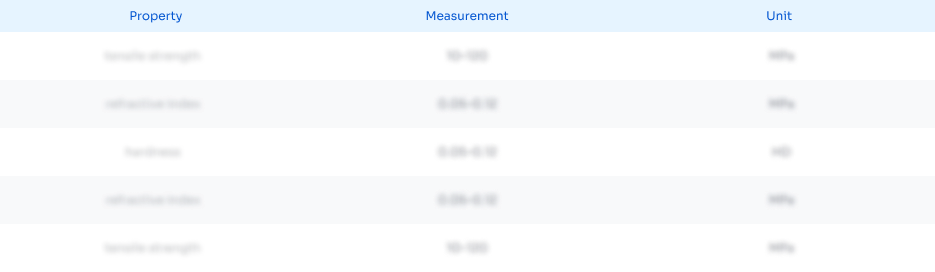
Abstract
Description
Claims
Application Information

- R&D
- Intellectual Property
- Life Sciences
- Materials
- Tech Scout
- Unparalleled Data Quality
- Higher Quality Content
- 60% Fewer Hallucinations
Browse by: Latest US Patents, China's latest patents, Technical Efficacy Thesaurus, Application Domain, Technology Topic, Popular Technical Reports.
© 2025 PatSnap. All rights reserved.Legal|Privacy policy|Modern Slavery Act Transparency Statement|Sitemap|About US| Contact US: help@patsnap.com