Carbon dioxide arc welding wire with small diameter of 1.6 mm and high alloy content
A carbon dioxide and gas protection technology, applied in welding medium, welding equipment, metal processing equipment, etc., can solve the problems of single formula, prone to spatter, reduce welding repair effect, etc., to achieve the effect of high alloy content and wide range of applications
- Summary
- Abstract
- Description
- Claims
- Application Information
AI Technical Summary
Problems solved by technology
Method used
Examples
example 1
[0011] A carbon dioxide gas shielded welding wire for blast furnaces in steel mills;
[0012] It consists of a 1.6mm wire sheath and a flux core which includes the following components: 4% C, 1.5% Si, 1.0% Mn, 22% Cr, 1.5% Ni, 3.5% Mo, 2% Co, 3.5% Nb, 1.5% V, 1.5% W, 3.5% Ti; the rest is B.
[0013] It has the advantages of high temperature resistance, corrosion resistance, wear resistance and high pressure resistance.
example 2
[0015] A carbon dioxide gas shielded welding wire used in cement mill grinding;
[0016] It includes a 1.6mm welding wire sheath and a flux core, which includes the following components: 5% C, 1.5% Si, 1.0% Mn, 22% Cr, 7% V, 7% Ti, and the rest is b.
[0017] It has the advantages of wear resistance, impact resistance and high temperature resistance.
example 3
[0019] A carbon dioxide gas shielded welding wire for oil drilling valves;
[0020] It includes a 1.6mm welding wire sheath and a flux core, which includes the following components: 1.0% C, 1.2% Si, 17% Mn, 12% Cr, 7% Ni, 5% Co, and the rest is b.
[0021] It has the advantages of corrosion resistance, high pressure resistance and high strength.
[0022] The present invention adopts the above formula, which contains various alloy elements and high alloy content, and is especially suitable for occasions requiring high temperature resistance, corrosion resistance, wear resistance and impact resistance, so that the flux cored wire can be used more widely.
PUM
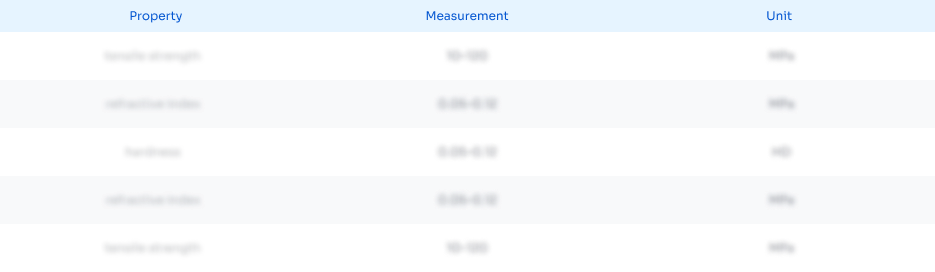
Abstract
Description
Claims
Application Information

- R&D
- Intellectual Property
- Life Sciences
- Materials
- Tech Scout
- Unparalleled Data Quality
- Higher Quality Content
- 60% Fewer Hallucinations
Browse by: Latest US Patents, China's latest patents, Technical Efficacy Thesaurus, Application Domain, Technology Topic, Popular Technical Reports.
© 2025 PatSnap. All rights reserved.Legal|Privacy policy|Modern Slavery Act Transparency Statement|Sitemap|About US| Contact US: help@patsnap.com