Motor drive device
A driving device and motor technology, applied in the direction of motor control, electric controller, electrical components, etc., can solve the problem of not providing
- Summary
- Abstract
- Description
- Claims
- Application Information
AI Technical Summary
Problems solved by technology
Method used
Image
Examples
Embodiment approach 1
[0023] Figure 1A It is a block diagram including the motor drive device 12 according to Embodiment 1 of the present invention.
[0024] Such as Figure 1A As shown, the position command Prc generated by the host controller 11 to indicate the position is input to the motor drive device 12 . The motor drive device 12 generates a drive signal Dd based on the position command Prc, and drives the motor 13 with the drive signal Dd. Thereby, the position of the movable part of the motor 13 is controlled. The encoder 14 detects the position of the movable portion thus controlled, and notifies the motor drive device 12 as motor position information Pd.
[0025] In addition, in the motor drive device 12 , the command response filter unit 21 smoothes the input position command Prc, and outputs the filtered position command, that is, the filtered position command Prf. This smoothing is achieved using a primary delay filter, a secondary filter, a moving average filter, or the like that ...
Embodiment approach 2
[0031] figure 2 It is a block diagram including the motor drive device 32 according to Embodiment 2 of the present invention.
[0032] exist figure 2 in, right with Figure 1A The same constituent elements are assigned the same reference numerals, and detailed description thereof will be omitted. figure 2 The motor driving device 32 of the second embodiment shown is equipped with Figure 1A In addition to the structure of , it also includes an evaluation index measurement unit 24 and a servo adjustment unit 15 .
[0033] The evaluation index measuring unit 24 receives the position command Prc and the motor position information Pd as input, and outputs an evaluation index.
[0034] In addition, the servo adjustment unit 15 changes the viscous friction coefficient Kw of the viscous friction calculation unit 23 , acquires the evaluation index obtained from the evaluation index measurement unit 24 every positioning operation, and determines the optimum value of the viscous fr...
Embodiment approach 3
[0057] Figure 8 It is a flowchart of viscous friction compensation processing executed by the servo adjustment unit 15 of the third embodiment.
[0058] Regarding steps 1, 2, 4, 4-1, and Figure 4 The same, but in the present embodiment, in step 3, the evaluation index measuring unit 24 measures the positioning settling time. In addition, after the trial times are executed, the viscous friction coefficient Kw that minimizes the positioning settling time is output in step 5 .
[0059] Thus, in the present embodiment, the servo adjustment unit 15 determines the optimum value of the viscous friction coefficient Kw so as to minimize the positioning settling time. Then, the servo adjustment unit 15 sets the optimum viscous friction coefficient Kw thus determined to the viscous friction calculation unit 23 .
[0060] In this method, with Figure 7 It can be seen from the change of the positioning settling time of , that the same viscous friction coefficient Kw=8 as in the secon...
PUM
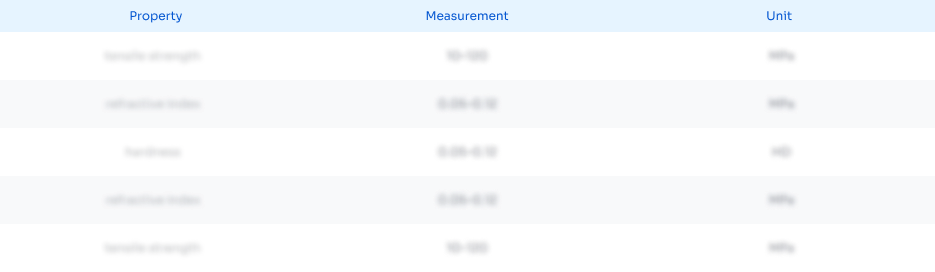
Abstract
Description
Claims
Application Information

- R&D
- Intellectual Property
- Life Sciences
- Materials
- Tech Scout
- Unparalleled Data Quality
- Higher Quality Content
- 60% Fewer Hallucinations
Browse by: Latest US Patents, China's latest patents, Technical Efficacy Thesaurus, Application Domain, Technology Topic, Popular Technical Reports.
© 2025 PatSnap. All rights reserved.Legal|Privacy policy|Modern Slavery Act Transparency Statement|Sitemap|About US| Contact US: help@patsnap.com