Spindle dynamic error and thermal deformation analyzer
A technology of dynamic error and thermal deformation, which is applied in the testing of instruments, measuring devices, mechanical parts, etc., to achieve the effects of easy tilting, good measurement accuracy and efficient tilting
- Summary
- Abstract
- Description
- Claims
- Application Information
AI Technical Summary
Problems solved by technology
Method used
Image
Examples
Embodiment 1
[0018] Such as figure 1 As shown, a spindle dynamic error and thermal deformation analyzer includes a shaft sleeve 4 and a sensor 3 arranged on the shaft sleeve 4, the sensor 3 is more than one, and the sensors 3 are all fixed on the side wall of the shaft sleeve 4 above, and the sensors 3 are all inductive sensors 3, and the measurement points of each sensor 3 are not located on the same straight line.
[0019] In this embodiment, the provided shaft sleeve 4 is used to fix each sensor 3. When the shaft sleeve 4 is sleeved on the main shaft, each sensor 3 forms a plurality of non-contact sensors 3 relative to the main shaft to be measured, so that , this structure can be more conveniently installed on the main shaft of the lathe to complete the dynamic error and thermal deformation analysis of the main shaft; furthermore, the sensor 3 is further limited by the electric induction sensor 3, which can make the sensor 3 work in a wet environment It can still ensure good measureme...
Embodiment 2
[0021] The present embodiment is further limited on the basis of embodiment 1, as figure 1 As shown, the further technical solution is: in order to facilitate the replacement of sensor 3 types or models according to specific measurement needs, the sensors 3 are provided with magnetic bases 1, and each sensor 3 is magnetically adhered to the sensor 3 by the magnetic base 1 on each On the shaft sleeve 4.
[0022] In order to make this structure have the function of braking the rotation of the main shaft, so as to enrich the scope of application of this structure, for example, it can be used for the test and analysis of a single main shaft that has been disengaged, and also includes a driving part 2 fixed at any end of the shaft sleeve 4 .
[0023] In order to facilitate the fixing of this structure, the base 1 is also fixed on the free end of the driving part 2 .
Embodiment 3
[0025] This embodiment is further limited on the basis of any one of the solutions provided by the above embodiments. In order to enable this structure to conveniently complete the measurement of the inclination and deflection of the main shaft, and the error analysis on the X-axis, Y-axis and Z-axis, the The number of sensors 3 is at least five.
PUM
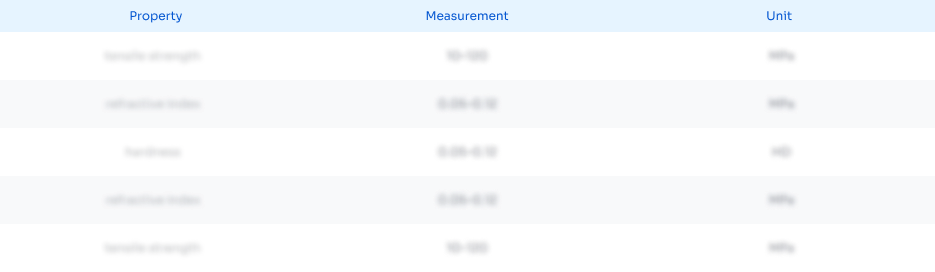
Abstract
Description
Claims
Application Information

- R&D Engineer
- R&D Manager
- IP Professional
- Industry Leading Data Capabilities
- Powerful AI technology
- Patent DNA Extraction
Browse by: Latest US Patents, China's latest patents, Technical Efficacy Thesaurus, Application Domain, Technology Topic, Popular Technical Reports.
© 2024 PatSnap. All rights reserved.Legal|Privacy policy|Modern Slavery Act Transparency Statement|Sitemap|About US| Contact US: help@patsnap.com