Method and device for producing dimethyl disulfide through oxidation of methyl mercaptan salt solution
A technology of dimethyl disulfide and methyl mercaptan, which is applied in the field of organic chemical industry, can solve the problems of high product purification cost, complex operating conditions, difficulty in controlling the degree of oxidation, etc., achieves continuous production and automatic control, and simple process flow , the effect of easy continuous production and automatic control
- Summary
- Abstract
- Description
- Claims
- Application Information
AI Technical Summary
Problems solved by technology
Method used
Image
Examples
Embodiment 1
[0028] In a 1000ml four-necked flask equipped with a magnetic stirrer, add 500ml of an aqueous solution containing 10% to 20%wt of sodium methyl mercaptide, 0.1% to 5%wt of free alkali (calculated as NaOH), and 50 to 150ppm of a Co catalyst, Under the conditions of heating and stirring in a water bath at 50°C to 100°C, pure oxygen was continuously introduced into the solution through the gas distribution head, and the reaction stopped after 60 minutes. g oil. After chromatographic analysis, the components of the oily substance are: 99.7% of dimethyl disulfide, 0.1% of methyl sulfide, and 0.2% of water.
Embodiment 2
[0030] In a simulated tower with a height of 4.5 meters, an inner diameter of 50 mm, and filled with saddle ring fillers and a hot water jacket, 5000 ml of industrial liquid caustic soda with 10% to 30% wt of sodium hydroxide is charged from the bottom of the tower to the liquid Methyl mercaptan gas is passed into the alkali to carry out absorption reaction, and the aeration is stopped when methyl mercaptan components appear in the tail gas at the top of the tower, and then 0.5-5g of Co-containing catalyst is dissolved in the solution, and then the gas is passed into the jacket of the simulated tower. Warm up the solution to 70°C with hot water, continuously feed oxygen-enriched air with an oxygen content of 25% to 80%wt into the solution from the bottom of the tower, keep the reaction pressure at 0.1 to 0.3MPa, and the temperature at 70 to 90°C; stop after 30 minutes Introduce oxygen-enriched air, cool down the simulated tower, take out the liquid in the tower and let it stand...
Embodiment 3
[0032] The remaining solution after the oxidation reaction in Example 2 was left to stand for stratification and liquid separation was reacted with an appropriate amount of methyl mercaptan to obtain an aqueous solution containing 5% to 25% wt of sodium methyl mercaptan and 10% to 20% wt of free alkali. This solution is sent in the simulated tower described in embodiment 2, under the condition of 80 ℃, 0.1MPa, pass through the oxygen-enriched air of oxygen content 25%~99%wt, after oxidation reaction 15 minutes, the simulated tower is cooled , The liquid in the tower was taken out and allowed to stand for stratification to obtain 471.0 g of oily substance, the components of which were 99.6% of dimethyl disulfide, 0.2% of methyl sulfide, and 0.2% of water. After rectification of the oil, a light yellow transparent liquid is obtained, and the components are 99.9% of dimethyl disulfide and 0.1% of water.
PUM
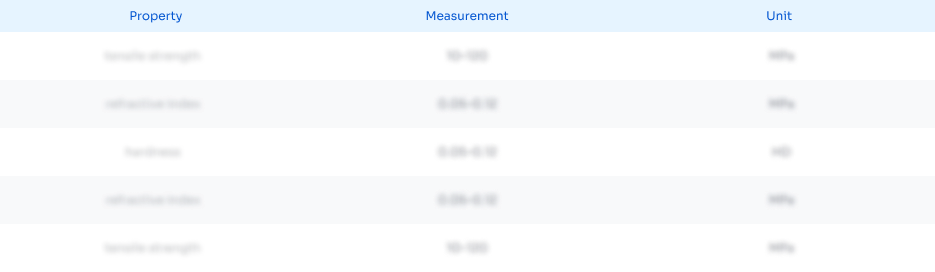
Abstract
Description
Claims
Application Information

- Generate Ideas
- Intellectual Property
- Life Sciences
- Materials
- Tech Scout
- Unparalleled Data Quality
- Higher Quality Content
- 60% Fewer Hallucinations
Browse by: Latest US Patents, China's latest patents, Technical Efficacy Thesaurus, Application Domain, Technology Topic, Popular Technical Reports.
© 2025 PatSnap. All rights reserved.Legal|Privacy policy|Modern Slavery Act Transparency Statement|Sitemap|About US| Contact US: help@patsnap.com