Method for producing fiberboard containing ultramicro amount of residual formaldehyde
A production method and residual technology, which are used in fiber raw materials, fiber raw material processing, pretreatment of molding materials, etc., can solve the problem that the formaldehyde emission of finished panels does not meet the standard requirements, and the difficulty of controlling the formaldehyde emission of finished panels increases. The proportion is difficult to achieve stability and other problems, to achieve the effect of improving adhesive properties, improving brittleness, and high bonding strength
- Summary
- Abstract
- Description
- Claims
- Application Information
AI Technical Summary
Problems solved by technology
Method used
Image
Examples
Embodiment l
[0032] A kind of production method of ultrafine formaldehyde residue fiberboard, it is characterized in that, production steps are as follows:
[0033] (1) Preparation of adhesive:
[0034] a. Raw materials in parts by weight: 50 parts of papermaking black liquor; 100 parts of phenolic resin; 1 part of γ-mercaptopropyl triethoxysilane as coupling agent; polyether modified polydimethylsiloxane as auxiliary agent 1 part; treatment agent ozone 1 part; spare;
[0035] b. Acid reaction stage: put the papermaking black liquor in parts by weight into the reaction kettle, start the agitator, add an aqueous solution of hydrochloric acid with a mass concentration of 25% while stirring to adjust the pH value of the solution to 4, start heating, and when the temperature stabilizes at React for 2 hours at 60°C;
[0036] c. Alkali reaction stage: after the acid reaction stage, immediately add phenolic resin, coupling agent KH-580 and auxiliary agent polyether modified polydimethylsiloxane...
Embodiment 2
[0048] A kind of production method of ultrafine formaldehyde residue fiberboard, it is characterized in that, production steps are as follows:
[0049] (1) Preparation of adhesive:
[0050] a. Raw materials in parts by weight: 200 parts of papermaking black liquor; 100 parts of phenolic resin; 4 parts of coupling agent γ-mercaptopropyltriethoxysilane; 4 parts of auxiliary agent 1,3-propanediol; 3 parts of treatment agent ADA ;spare;
[0051] b. Acid reaction stage: put the papermaking black liquor in parts by weight into the reactor, start the agitator, add a sulfuric acid aqueous solution with a mass concentration of 27% while stirring to adjust the pH value of the solution to 5, start heating and heat up, when the temperature stabilizes at Reaction at 70°C for 1.4h;
[0052] c. Alkali reaction stage: After the acid reaction stage is over, immediately add phenolic resin, coupling agent KH-590 and auxiliary agent 1,3-propanediol in parts by weight, and add NaOH aqueous solut...
Embodiment 3
[0063] A kind of production method of ultrafine formaldehyde residue fiberboard, it is characterized in that, production steps are as follows:
[0064] (1) Preparation of adhesive:
[0065] a, raw materials in parts by weight: 350 parts of papermaking black liquor; 100 parts of phenolic resin; 8 parts of coupling agent γ-mercaptopropyltrimethoxysilane; 8 parts of N-methylpyrrolidone solution of auxiliary agent modified polyurea ; 2 parts of treatment agent PDS, 2 parts of ADA; standby;
[0066] b. Acid reaction stage: put the papermaking black liquor in parts by weight into the reaction kettle, start the agitator, add an aqueous solution of hydrochloric acid with a mass concentration of 28% while stirring to adjust the pH value of the solution to 7, start heating, and when the temperature stabilizes at Reaction at 80°C for 0.9h;
[0067] C, alkali reaction stage: after the acid reaction stage finishes, add the phenolic resin, coupling agent and auxiliary agent of parts by we...
PUM
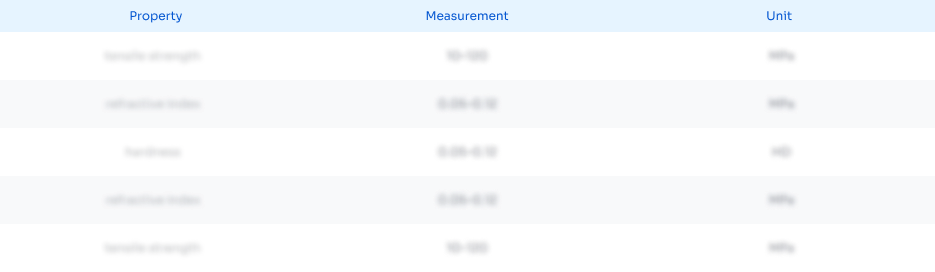
Abstract
Description
Claims
Application Information

- Generate Ideas
- Intellectual Property
- Life Sciences
- Materials
- Tech Scout
- Unparalleled Data Quality
- Higher Quality Content
- 60% Fewer Hallucinations
Browse by: Latest US Patents, China's latest patents, Technical Efficacy Thesaurus, Application Domain, Technology Topic, Popular Technical Reports.
© 2025 PatSnap. All rights reserved.Legal|Privacy policy|Modern Slavery Act Transparency Statement|Sitemap|About US| Contact US: help@patsnap.com