GaAs (111) wafer cleaning method
A wafer, hydrochloric acid technology, applied in the direction of electrical components, semiconductor/solid-state device manufacturing, circuits, etc., can solve the problems of destroying the surface morphology of the substrate, irregular natural oxide layer, and inability to obtain effects.
- Summary
- Abstract
- Description
- Claims
- Application Information
AI Technical Summary
Problems solved by technology
Method used
Image
Examples
Embodiment 1
[0032] 1) The GaAs(111)A substrate was ultrasonically cleaned with acetone and ethanol in sequence, and the ultrasonic time was 10 minutes to remove oil and organic matter on the substrate surface;
[0033]2) Soak the substrate obtained in step 1) in hydrogen peroxide with a mass concentration of 30% for 2 minutes, take it out, and wash it in deionized water for 30 seconds; after taking it out, soak it in hydrochloric acid with a mass concentration of 10% for 1 min , take it out, wash it in deionized water for 30s, take out the substrate and repeat the steps of soaking in hydrogen peroxide—cleaning in deionized water—soaking in hydrochloric acid—cleaning in deionized water 4 times (that is, soaking in hydrogen peroxide—cleaning in deionized water—soaking in hydrochloric acid—deionized water Cleaning step cycle 5 times), after completing the last deionized water cleaning, blow dry with nitrogen;
[0034] 3) Place the GaAs(111) substrate obtained after the treatment in step 2) i...
Embodiment 2
[0042] 1) The GaAs(111)B substrate is ultrasonically cleaned with acetone and ethanol in sequence, and the ultrasonic time is 5 minutes and 15 minutes respectively, to remove oil and organic matter on the surface of the substrate;
[0043] 2) Soak the substrate obtained in step 1) in hydrogen peroxide with a mass concentration of 25% for 3 minutes, take it out, and wash it in deionized water for 30 seconds; after taking it out, soak it in hydrochloric acid with a mass concentration of 13% for 2 minutes, take it out , wash in deionized water for 30s, take out the substrate and repeat the steps of soaking in hydrogen peroxide-cleaning in deionized water-soaking in hydrochloric acid-cleaning in deionized water twice, after the last deionized water cleaning, blow dry with nitrogen;
[0044] 3) Place the GaAs(111) substrate obtained after the treatment in step 2) in (NH 4 ) 2 Passivate in S solution for 20 minutes, take it out, wash it in deionized water for 30 seconds, and dry it...
Embodiment 3
[0047] 1) The GaAs(111)A substrate was ultrasonically cleaned with acetone and ethanol in sequence, and the ultrasonic time was 10 minutes to remove oil and organic matter on the substrate surface;
[0048] 2) Soak the substrate obtained in step 1) in hydrogen peroxide with a mass concentration of 35% for 5 minutes, take it out, and wash it in deionized water for 30 seconds; after taking it out, soak it in hydrochloric acid with a mass concentration of 8% for 3 minutes, take it out , wash in deionized water for 60s, take out the substrate and repeat the steps of soaking in hydrogen peroxide-cleaning in deionized water-soaking in hydrochloric acid-cleaning in deionized water 3 times, after the last deionized water cleaning, blow dry with nitrogen;
[0049] 3) Place the GaAs(111) substrate obtained after the treatment in step 2) into (NH 4 ) 2 Passivate in S solution for 10 minutes, take it out, wash it in deionized water for 30 seconds, and dry it with nitrogen.
PUM
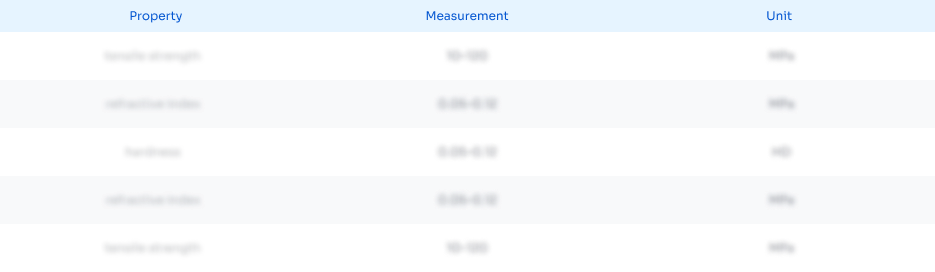
Abstract
Description
Claims
Application Information

- R&D
- Intellectual Property
- Life Sciences
- Materials
- Tech Scout
- Unparalleled Data Quality
- Higher Quality Content
- 60% Fewer Hallucinations
Browse by: Latest US Patents, China's latest patents, Technical Efficacy Thesaurus, Application Domain, Technology Topic, Popular Technical Reports.
© 2025 PatSnap. All rights reserved.Legal|Privacy policy|Modern Slavery Act Transparency Statement|Sitemap|About US| Contact US: help@patsnap.com