Preparation method for refining slag for smelting bearing steel
A technology for refining slag and bearing steel, applied in the field of iron and steel metallurgy
- Summary
- Abstract
- Description
- Claims
- Application Information
AI Technical Summary
Problems solved by technology
Method used
Image
Examples
Embodiment 1
[0013] The slag components are: CaO38%, SiO 2 10%,Al 2 o 3 39%, MgO8%, CaF 2 5%, Ca / Al=1.0.
[0014] Taking the production of 1 ton of refining slag as an example, according to the composition of the slag system and the percentage by weight, use a weighing device to accurately weigh the mineral raw materials of each component. The weights are: lime 391.75kg, river sand 125.00kg, grade Bauxite 433.33kg, magnesite 160.00kg, fluorite 58.82kg. Use a crusher to crush the weighed raw materials and process them accordingly. Use a ball mill to fully mix the weighed components for 1.3 hours. Put the mixed slag material into the slag melting furnace, the initial temperature is 1330°C, and the slag material is completely melted. After the slag is completely melted, it is taken out and poured into the granulation tank for water quenching. After cooling, it is taken out, dried and stored in bags.
Embodiment 2
[0016] The slag system components are: CaO56%, SiO 2 5%,Al 2 o 3 28%,MgO5%,CaF 2 6%, Ca / Al=2.0.
[0017] Taking the production of 1 ton of pre-melted slag as an example, according to the composition of the slag system and the percentage by weight, the mineral raw materials of each component are accurately weighed with a weighing device. The weights are respectively: lime 577.32kg, river sand 62.50kg, a Grade bauxite 311.11kg, magnesite 100.00kg, fluorspar 70.59kg. Use a crusher to crush the weighed raw materials and process them accordingly. Use a ball mill to fully mix the weighed components for 1.2 hours. Put the mixed slag material into the slag melting furnace, the initial temperature is 1360°C, and the slag material is completely melted. After the slag is completely melted, it is taken out and poured into the granulation tank for water quenching. After cooling, it is taken out, dried and stored in bags.
Embodiment 3
[0019] The slag system components are: CaO40%, SiO 2 6%,Al 2 o 3 48%,MgO2%,CaF 2 4%, Ca / Al=0.8.
[0020] Taking the production of 1 ton of pre-melted slag as an example, according to the composition of the slag system and the percentage by weight, the mineral raw materials of each component are accurately weighed with a weighing device. The weights are respectively: lime 412.37kg, river sand 75.00kg, Grade bauxite 533.33kg, magnesite 40.00kg, fluorite 47.06kg. Use a crusher to crush the weighed raw materials and process them accordingly. Use a ball mill to fully mix the weighed components for 1.4 hours. Put the mixed slag material into the slag melting furnace, the initial temperature is 1350°C, and the slag material is completely melted. After the slag is completely melted, it is taken out and poured into the granulation tank for water quenching. After cooling, it is taken out, dried and stored in bags.
PUM
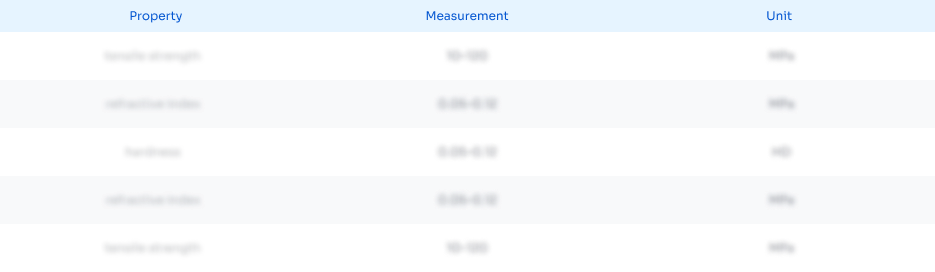
Abstract
Description
Claims
Application Information

- R&D Engineer
- R&D Manager
- IP Professional
- Industry Leading Data Capabilities
- Powerful AI technology
- Patent DNA Extraction
Browse by: Latest US Patents, China's latest patents, Technical Efficacy Thesaurus, Application Domain, Technology Topic, Popular Technical Reports.
© 2024 PatSnap. All rights reserved.Legal|Privacy policy|Modern Slavery Act Transparency Statement|Sitemap|About US| Contact US: help@patsnap.com