Method for preparing epoxy flax oil plasticizers
The technology of epoxy linseed oil and plasticizer is applied in the field of material additives, which can solve the problems of low temperature of synthetic products and easy corrosion of equipment, and achieve the effects of good plasticization, simple production steps and cost saving.
- Summary
- Abstract
- Description
- Claims
- Application Information
AI Technical Summary
Problems solved by technology
Method used
Examples
example 1
[0018] Take 1L of distilled water and place it in an ice-salt bath to cool down. When the temperature is 0°C, connect the gas outlet of the ozone generator to the sand filter head with a polytetrafluoroethylene rubber tube, and rinse the sand filter head with distilled water for 5 times, and then Put it in distilled water, seal the water surface with a polyethylene film, turn on the ozone generator for 30 minutes to prepare ozone distilled water, and quickly place it in an insulated bucket filled with liquid nitrogen to freeze it quickly to obtain ozonated water. Ice, for subsequent use; by weight fraction, select 5 parts of formic acid aqueous solution with a mass fraction of 60%, 45 parts of sherwood oil and 50 parts of linseed oil, and mix and stir them evenly at 20°C, with a stirring speed of 800r / min, after mixing and stirring for 5 minutes, place it in a 90°C constant temperature water bath at a speed of 1200r / min, stir and mix until the temperature of the mixed solutio...
example 2
[0020] Take 1.5L of distilled water and place it in an ice-salt bath to cool down. When the temperature is 2°C, connect the gas outlet of the ozone generator to the sand filter head with a polytetrafluoroethylene rubber tube, and rinse the sand filter head with distilled water 5 times. Then put it in distilled water, seal the water surface with a polyethylene film, turn on the ozone generator for 40 minutes to prepare ozone distilled water, and quickly place it in an insulation bucket filled with liquid nitrogen to freeze it quickly to obtain ozone Melt ice and set aside; in terms of weight fraction, respectively select 10 parts of formic acid aqueous solution with a mass fraction of 60%, 40 parts of petroleum ether and 50 parts of linseed oil, and mix and stir them evenly at 25 ° C, and the stirring speed is 900 r / min, after it was mixed and stirred for 8 minutes, it was placed in a 95°C constant temperature water bath at a speed of 1300r / min, and stirred and mixed until th...
example 3
[0022] Put 2L of distilled water in an ice-salt bath to cool down. When the temperature is 5°C, connect the gas outlet of the ozone generator to the sand filter head with a Teflon rubber tube, and rinse the sand filter head with distilled water for 6 times, and then Put it in distilled water, seal the water surface with a polyethylene film, turn on the ozone generator for 60 minutes to prepare ozone distilled water, and quickly place it in an insulated bucket filled with liquid nitrogen to freeze it quickly to obtain ozonated water. Ice, for subsequent use; by weight fraction, choose 20 parts of formic acid aqueous solution with a mass fraction of 60%, 35 parts of sherwood oil and 45 parts of linseed oil, and mix and stir them evenly at 30°C, with a stirring speed of 1000r / min, after mixing and stirring for 10 minutes, place it in a constant temperature water bath at 100°C at a speed of 1500r / min, stir and mix until the temperature of the mixed solution is 95°C; after the te...
PUM
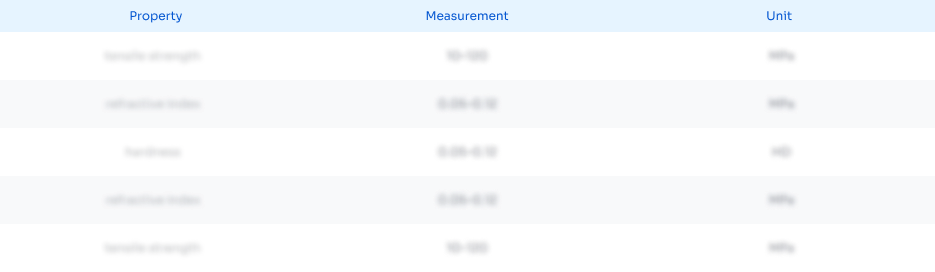
Abstract
Description
Claims
Application Information

- R&D Engineer
- R&D Manager
- IP Professional
- Industry Leading Data Capabilities
- Powerful AI technology
- Patent DNA Extraction
Browse by: Latest US Patents, China's latest patents, Technical Efficacy Thesaurus, Application Domain, Technology Topic, Popular Technical Reports.
© 2024 PatSnap. All rights reserved.Legal|Privacy policy|Modern Slavery Act Transparency Statement|Sitemap|About US| Contact US: help@patsnap.com