Injection molding process of metal powder metallurgical workpiece
An injection molding process and powder metallurgy technology, applied in the field of metal powder metallurgy, can solve problems such as poor hardness
- Summary
- Abstract
- Description
- Claims
- Application Information
AI Technical Summary
Problems solved by technology
Method used
Image
Examples
Embodiment 1
[0029] Step 1: Injection molding, the mixture of metal powder and organic binder is injection molded into an injection base through an injection molding machine; wherein, the metal powder is composed of iron, nickel, carbon, and in every 100 parts by weight of metal, nickel: 7.75 parts, 0.3 parts of carbon, and the balance of iron, the organic binder is specifically a polymer material, and the weight ratio of the metal powder and the organic binder is 80:20.
[0030] Step 2: remove the organic binder, and remove the organic binder in the injection mold by thermal decomposition;
[0031] The degreasing temperature is 110±10°C, the time is 660min, the speed of the nitric acid pump is 70 rpm; the degreasing nitrogen flow rate is 2.5-3.0m3 / h, the blowing nitrogen flow rate is 2.5-3.0m3 / h, and the nitric acid concentration is 98% mole percent;
[0032] Specifically, the product is neatly placed into the furnace with carbon plates, and the adhesive inside the blank is removed by usi...
Embodiment 2
[0042] Step 1: Injection molding, the mixture of metal powder and organic binder is injection-molded into an injection base through an injection molding machine; wherein, the metal powder is composed of iron, nickel, carbon, and in every 100 parts by weight of metal, nickel: 8.25 parts, 0.3 parts of carbon, and the balance of iron, the organic binder is specifically a polymer material, and the weight ratio of the metal powder and the organic binder is 89:11.
[0043] Step 2: remove the organic binder, and remove the organic binder in the injection mold by thermal decomposition; the specific method is as in Example 1;
[0044] Step 3: Sintering, sintering the injection blank, the sintering temperature is as follows.
[0045]
[0046] Step 4: Quenching, at 900-1000°C, in CO 2 Quenching in an atmosphere for 2.5 hours;
[0047] Step 5: Tempering, at 150-250°C, tempering for 1 hour. to get the finished product.
Embodiment 3
[0049] Step 1: Injection molding, the mixture of metal powder and organic binder is injection molded into an injection blank through an injection molding machine; wherein, the metal powder is composed of iron, nickel, carbon, and in every 100 parts by weight of metal, nickel: 8 parts, 0.35 parts of carbon, and the balance of iron, the organic binder is specifically a polymer material, and the weight ratio of the metal powder and the organic binder is 85:15.
[0050] Step 2: remove the organic binder, and remove the organic binder in the injection mold by thermal decomposition; the specific method is as in Example 1.
[0051] Step 3: Sintering, sintering the injection blank, the sintering temperature is as follows.
[0052]
[0053] Step 4: Quenching, at 900-1000°C, in CO 2 Quenching in an atmosphere for 1.5 hours;
[0054] Step 5: Tempering, at 150-250°C, tempering for 2 hours. to get the finished product.
PUM
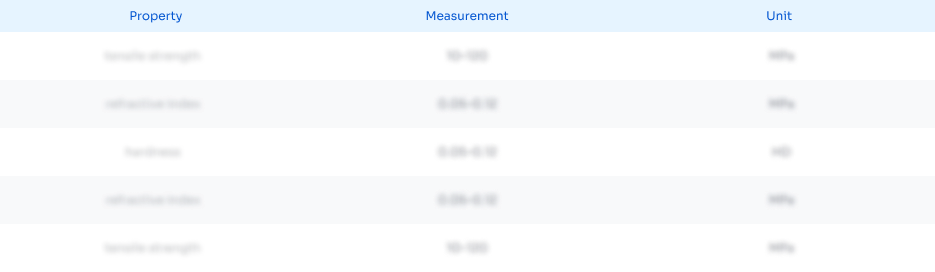
Abstract
Description
Claims
Application Information

- R&D
- Intellectual Property
- Life Sciences
- Materials
- Tech Scout
- Unparalleled Data Quality
- Higher Quality Content
- 60% Fewer Hallucinations
Browse by: Latest US Patents, China's latest patents, Technical Efficacy Thesaurus, Application Domain, Technology Topic, Popular Technical Reports.
© 2025 PatSnap. All rights reserved.Legal|Privacy policy|Modern Slavery Act Transparency Statement|Sitemap|About US| Contact US: help@patsnap.com